When we think about green buildings, we imagine clean-cut modern designs, spacious aired lobbies, solar panels installed on rooftops, large windows, and vertical gardens. But the hard truth is that what makes a building green is not just its final look.
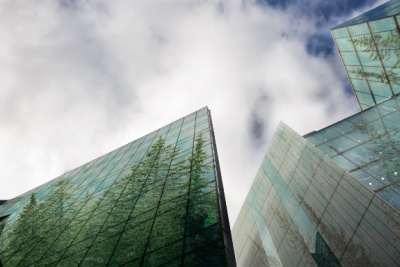
The World Green Building Council explains that buildings account for 39% of global energy-related carbon emissions. Twenty-eight percent of those emissions happen after buildings are inaugurated, opened, and operating, demanding energy to heat, cool, and power them. An astounding 11% of the sector’s carbon emissions are linked to the manufacturing process of materials—steel, cement, or glass—and construction.
From sourcing raw materials to groundbreaking to certifications, buildings will only be green if the materials used and the machinery employed are sustainable. But this level of change requires a shift in mentality, concepts, and technologies.
Talk Sustainability Early in the Meetings
When the word “sustainability“ comes into play in the early stages of a development project, executives and contractors will immediately think about one thing: upfront costs.
Whether it may be turning to locally sourced materials to reduce the carbon footprint of transportation costs, switching to novel low-carbon materials, or substituting steel, concrete, wood, and bricks for recycled alternatives, it is no secret that green means more money.
But does the investment pay off and are leaders in the industry going down this road? The U.S. Green Building Council’s (USGBC) 2023 Green Building Trends and Sentiments report shows that sustainability, human health, decarbonization, energy efficiency, and net zero are top of mind in the industry. The USGBC surveyed over 500 leading members of the green building community to gain insight on their views.
Respondents say that the main barriers for green buildings are lack of funding and lack of knowledge. They recognized as critical the ability to select healthy materials, use durable and low-maintenance materials, and integrate circular economy principles.
The economic benefits of sustainable materials are also found in their structural strengths. Recycled and green materials are usually more durable, reducing maintenance costs. They are also more energy efficient, dramatically cutting electric bills associated with heating and cooling buildings.
Beyond materials, the importance of sustainability for consumers is driving demand. This demand for green buildings is estimated to drive growth at a CACGR of 9.50%, reaching $1312.12 billion by 2030, according to Market Research Future.
Owners are also reaping the benefits of sustainable building practices. After analyzing 20,000 U.S. office buildings in late 2022, CBRE found that the average rent of offices with Leadership in Energy and Environmental Design (LEED) certification is 31% higher than that of non-LEED-certified buildings.
As green buildings build brand reputation, generate trust, and inspire communities, the scientific community has established health, wellness, and productivity gains for those living and working in them. A recent WELL research study found that better air quality can generate an 8% uptick in employee performance, and green certifications can lead to a 28% improvement in overall satisfaction with the workplace.
By creating natural environments that offer higher air quality standards and are pollutant-free, green buildings can reduce stress and support a healthier community.
Sustainable Heavy Machinery
Similarly, in those early meetings of construction projects, the same thoughts occur when decision-makers talk about using sustainable heavy machinery. However, the upfront costs of such equipment are not always as expensive as people might imagine. For example, second-hand heavy machinery, which can be in excellent condition, can also be more sustainable and economically friendly than new traditional machines.
Additionally, as sustainable heavy machinery technology advances, the industry will likely see its costs decrease and availability rise.
For example, electric excavators and hydrogen-powered cranes are more popular today than ever and have excellent performance and efficiency rates, all while generating zero tailpipe emissions and less noise contamination.
Using sustainable heavy machinery can drastically reduce operational costs, as it uses less or no fuel at all and requires little maintenance. Sustainable machinery can also be more productive and easier to operate.
The Tools of the Global Digital Transformation
When it comes to sustainability, costs, performance, and benefits, no technology is doing more for the industry than the tools of the global digital transformation.
From cloud to edge computing to Industrial Internet of Things (IIoT) devices, telematics, cameras, sensors, and digital twins, builders can now have full control and visualization of their projects. This allows them to leverage data-driven analytics, increase performance, reduce emissions, train workers faster, run simulations, smooth out supply chains, identify risks, and prevent accidents.
By turning to modern technologies and sustainable machinery, companies that reduce the risks of accidents and increase safety will see positive impacts for their workers, their business reputation, less downtime, and lower insurance costs.
But keeping an eye on the news for innovation in construction is also critical in this day and age. The industry is in full transformative swing, reimaging operations, tools, technologies, machinery, designs, and raw materials. In simple words, sustainability and innovation are not one-and-done. They are a continual work in progress.
So, the next time the word “sustainability” comes up early in the first meetings of your new construction project, remember that, yes, costs are an essential discussion to have. But when it comes to going green, costs can only be assessed when balancing the long-term return.
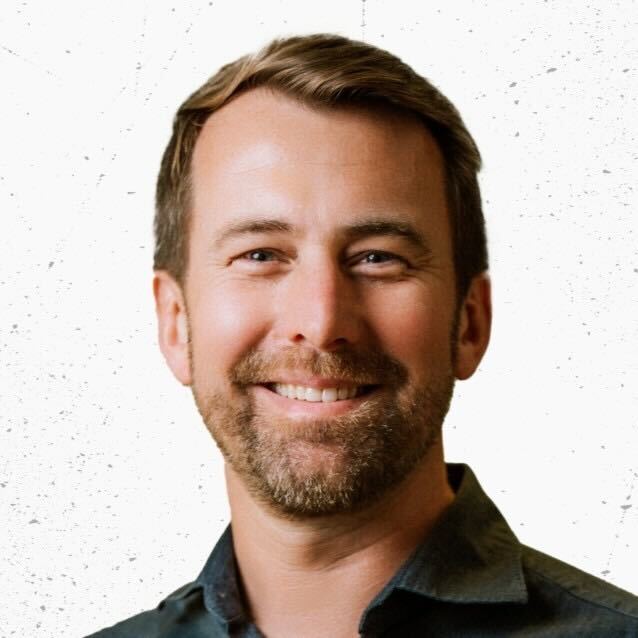
Aaron Kline is co-founder and COO of Boom & Bucket, an online platform for buying and selling used heavy equipment. He holds an MBA from Stanford University Graduate School of Business and a bachelor’s degree from Auburn University.