Hurricanes present wide-ranging hazards for facility managers and their teams to navigate during and after they strike populated areas and critical infrastructures.
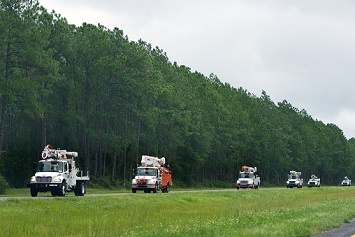
Bastiaan Slabbers / iStock Unreleased / Getty Images
OSHA states that following Hurricanes Katrina, Rita, and Wilma in 2005, agency staff in Louisiana, Mississippi, Alabama, Florida, and Texas assisted emergency responders, search and rescue personnel, power restoration crews, and other response and recovery workers. As part of this work, OSHA’s staff collected data about working conditions and the safety and health of workers at a number of facilities.
Also, during its work, OSHA investigated 18 work-related deaths. There was no dominant single cause for the fatalities; the tragedies occurred when workers were struck by falling objects, fell from roofs, were struck by vehicles, were crushed by vehicles that rolled over, were electrocuted, died from burns during electrical utility work, and were overcome by toxic gases, among others.
Most Common Activities
- Roof inspection, tarping, and repair—identified in 26% of interventions. Three worker fatalities occurred during roof inspection, tarping, and repair. Two people were killed when, in separate incidents, they fell through holes in the roofs they were repairing. A third person also died from a fall.
- Debris collection and removal—identified in 26% of interventions. Two worker fatalities occurred during debris collection and removal. One person was struck by an out-of-control vehicle that entered a properly controlled and well-marked work zone. An equipment operator was killed when his tractor overturned into a ditch and pinned him underwater.
- Tree trimming—identified in 8% of interventions. No worker fatalities were reported during tree trimming.
- Restoring electrical utilities—identified in 7% of interventions. Three worker fatalities occurred during electrical utility restoration. One person was struck by a 75-foot utility pole that fell when it was being positioned with a forklift. One person was electrocuted when he contacted a live 110-volt line that he was attaching to a house. One person suffered fatal burns when the electrical system being restored became energized, exploded, and caused a flash fire.
- Debris reduction, recycling, and disposal—identified in 6% of interventions. Two worker fatalities occurred during these activities. One person was killed when he was struck by a bulldozer at a debris reduction site. One operator was killed when his excavator rolled down the debris pile he was working on.
- Assessment, cleanup, and facility repair—identified in 2% of interventions. Two worker fatalities occurred during these activities. One worker received an electrical shock when the knife he was using contacted a power line and he fell 18 feet. Another worker was killed when he was struck by a falling security gate that was damaged during a hurricane.
- Restoring communications systems—identified in 2% of interventions. Two worker fatalities occurred during this activity. One cable television repairman was electrocuted when he contacted a live electrical line 3 feet (ft) above the cable line he was working on. Another telecommunications worker was found dead near a ladder that was placed against a telephone pole.
- Restoring water and sewer services—identified in 1% of interventions. No worker fatalities were reported from this activity.
PeskyMonkey / iStock / Getty Images Plus / Getty Images
Most Frequently Observed Hazards
Work zone safety concerns—found at approximately 40% of sites. Many entries involved tree trimming or electrical line repair on or near roads. OSHA specialists often noted inadequate cones and other barriers at a work zone, improper use or lack of traffic control signs (e.g., directional arrows, flaggers with stop/slow signs), workers standing in areas where they were exposed to oncoming traffic, and absence of American National Standards Institute (ANSI)-approved high-visibility safety apparel such as vests and gloves.
“Employers need to ensure that workers establish work zones and traffic controls where multiple pieces of heavy equipment, vehicles, and workers are in close proximity,” states OSHA. “Work zones must be well marked with barriers, cones, signs, and flaggers to provide plenty of warning and appropriate direction to approaching vehicles.”
Improper use or lack of personal protective equipment (PPE)—found at approximately 35% of sites. Roughly 65% of the PPE entries reference a lack of face and head protection or the improper use of PPE. Entries indicated that individuals were not using goggles, hard hats, or face shields when those types of PPE were necessary. Other types of PPE commonly mentioned include hand protection (e.g., use of reinforced gloves during the handling of debris or insulating gloves when working around electrical lines), hearing protection, and body protection (e.g., chaps to protect the worker’s legs when operating a chain saw or ANSI-approved high-visibility vests in high traffic areas). Approximately 15% of all entries discussed fall protection use while operating aerial lifts.
“Employers should ensure that the JHA for each response and recovery task identifies the PPE needed for worker protection,” states OSHA. “Employers must provide properly fitting PPE to workers, train them how to use it, and ensure they use it when performing the task.”
Fall hazard/inadequate fall protection—identified at approximately 35% of sites. Common examples included using ladders that were not properly secured or did not extend 3 ft above the landing; structures such as towers used in debris removal sites or scaffolds that did not have adequate guardrails; and individuals not properly protected from falls when on roofs, handling debris on trucks, or using aerial lifts to trim trees or repair utilities. Entries frequently mentioned lack of or improper use of fall protection equipment (i.e., harnesses, lanyards, connectors, and suitable anchorage points).
“Employers must identify potential fall hazards associated with a task and ensure that these hazards are addressed through controls such as guardrails, a safety monitoring system that includes monitors and warning lines, and/or fall protection equipment,” says OSHA.
Struck by another object—identified at approximately 20% of sites. Hazards mentioned included materials falling from roofs or falling while being moved by heavy equipment, such as dump trucks, cranes, or grapplers.
“Employers need to ensure that appropriate precautions are taken such as securing equipment on elevated surfaces, using spotters around heavy equipment, and precluding workers from entering debris-handling zones,” states OSHA. “Employers must train workers to recognize and avoid these hazards and wear hard hats where overhead hazards exist.”
Aerial lifts and inadequate fall protection—approximately 15% of all entries discussed fall protection and other PPE use while operating aerial lifts. Almost all the entries identified a lack of or improper use of fall protection equipment by operators.
“Employers need to ensure that workers comply with the requirements of 29 CFR 1926.453, including the use of a properly anchored harness for fall protection,” said OSHA.
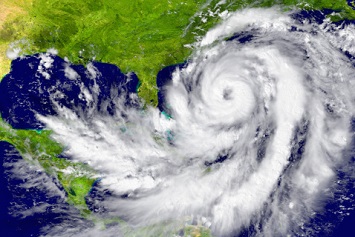
Harvepino / iStock / Getty Images Plus / Getty Images
Noise and Air
During its interventions, OSHA also collected data on worker exposure to noise and air contaminants. Briefly, the data show the following:
- Noise—20% of the 324 workers evaluated experienced noise exposure above OSHA’s permissible exposure limit (PEL) of 90 A-weighted decibels (dBA). Over 40% of the sampled workers were exposed to noise levels of 85 dBA or higher. Hazardous levels of noise exposure were particularly common among response and recovery workers involved in debris collection and reduction, site clearing, and transportation restoration activities. Some of the highest noise exposures were associated with operating heavy equipment, chippers, chain saws, and industrial vacuums. These overexposed workers must wear earplugs or earmuffs to help prevent hearing loss. When workers are exposed to hazardous levels of noise, employers must enroll the workers in a hearing conservation program, similar to the one outlined in OSHA’s standard on occupational noise exposure (29 CFR 1910.95(c)).
- Air contaminants. OSHA specialists tested for dust, silica, asbestos/total fibers, gas and vapor, and airborne metals. Among the findings:
- Heavy equipment operators were the group most consistently exposed to high levels of dust.
- Workers with elevated silica exposures were likely performing activities such as jack hammering or sawing road surfaces and building materials, moving and dumping dry concrete and brick rubble, or crushing silica containing debris under heavy equipment.
- Although asbestos was found in less than 1% of the samples evaluated during this phase of hurricane response and recovery, the risk could be higher during later phases when more workers are involved in building demolition.
- Carbon monoxide levels exceeded the action level in 17% of the 51 samples collected. Possible sources of exposure include emergency power generators used in poorly ventilated areas and gas-powered saws in need of service. On-site support workers (e.g., inspectors and engineers) had the highest carbon monoxide exposure levels among the workers evaluated.
- Workers were rarely exposed to hazardous levels of airborne metals (e.g., metal dust or fumes). Only one of the 1,240 results for metals exceeded the action level. That individual, exposed to copper fume, was involved in debris reduction activities. Exposure to copper fumes could result from hot work such as cutting and welding. No metal was detected in 97% of the air sample results OSHA obtained.