Weather, structural movement, and stress are constantly attacking your commercial roof. While normal aging will occur on all roofs, problems stemming from neglect, abuse, contamination, or accidents, if not detected early, can result in extensive, costly repairs or premature failure of the roofing system.
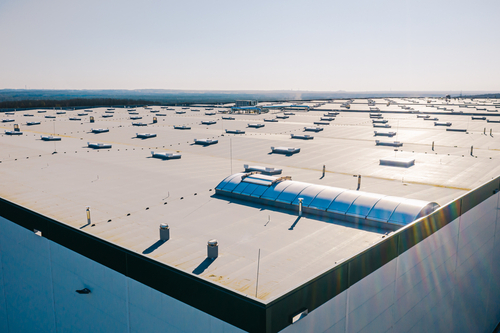
Plan and start an inspection program during the first year your roof has been installed. An essential element of a good inspection and maintenance program is proper record keeping and documentation. It is recommended to restrict access to your roof and create a maintenance log to keep track of who has access. You can add years to the life of your property’s roof by inspecting it regularly to detect minor problems before they become serious.
Roofing Maintenance Best Practices
- Have someone specially trained in your roof’s materials, whether single-ply or a particular coating, inspect the roof at least twice a year and after major weather events.
- You must provide walkways if people are on the roof regularly or if those servicing rooftop equipment like HVAC units and antennas are scheduled to maintain it every 30 days or more often. Exercise caution when not walking on walkways, especially on white membranes, as ice or frost buildup may not be visible. All membranes are slippery when wet.
- When workers must service rooftop equipment, they should use walkways and be careful not to puncture the roofing membrane with their tools and equipment.
- For thermoplastic polyolefin (TPO) and polyvinyl chloride (PVC) roofing, regularly remove animal fat/grease accumulation and clean the surface, either with a mixture of warm soap and water and/or by other approved cleaning methods.
- For rubber—ethylene propylene diene terpolymer (EPDM)—roofing membranes, do not exhaust kitchen wastes like vegetable oil or other animal fats directly onto the roof surface. If incidental contact is likely, contact the roofing system manufacturer for recommendations on membrane type and usage.
- Keep all petroleum products like solvents, grease, and oils off the membrane to avoid degradation.
- Keep the roof surface clean, especially at drain areas to avoid clogging. Drain ponding water from the roof within 48 hours of rain.
- Clean handprints, footprints, general traffic grime, industrial pollutants, and environmental dirt by scrubbing with detergent and water and then rinsing with clean water. To maximize reflectivity, clean white membranes every two years.
- Contact the manufacturer of any chemicals that come into contact with the roofing membrane. Some chemicals could degrade the membrane or cause swelling.
Roofing Repair Best Practices
Even if you maintain your roof and have it inspected regularly, flying debris, workers servicing equipment, and other factors can damage it. Here’s what to do if damage occurs.
- Soft or warped insulation may indicate a water leak. If there is a leak, locate it and determine if it is in the roof membrane, a wall, a curb, a skylight, or metal ductwork, or if it is a plumbing issue.
- Use lap sealant or any construction-grade caulk to make temporary repairs. Do not use roof cement to repair rubber (EPDM) membranes. Roof cement contains petroleum products that may degrade the membrane.
- Contact the membrane manufacturer to report the leak if the roof is still under warranty.
Benefits of Preventative Rooftop Maintenance
A proactive maintenance program provides many benefits for a commercial building. A Roofing Industry Alliance for Progress study examining low-slope roof systems found that roofs with robust maintenance programs lasted an average of 21 years while roofs that were not proactively maintained lasted only 13 years.
The study also noted a huge cost consideration: An actively maintained, 10,000-square-foot roof would cost an average of $1,400 per year, whereas a roof that was not proactively maintained would cost $2,500 a year. That’s a nearly $20,000 savings over the life of the roof, thanks to a proactive maintenance plan.
Emma Nealy is marketing manager of Versico Roofing Systems. The company was formed in 1993 when its owners acquired a major single-ply roofing company. Now, nearly 30 years later, Versico has positioned itself as one of the top single-ply roofing system manufacturers in the U.S.