As buildings become more complex, facility managers will need to leverage the best techniques available to handle the various challenges of keeping their facilities functional, safe, and liveable. But first, they’ll need to identify the unique issues in each property, then determine the most efficient ways to track and tackle them.
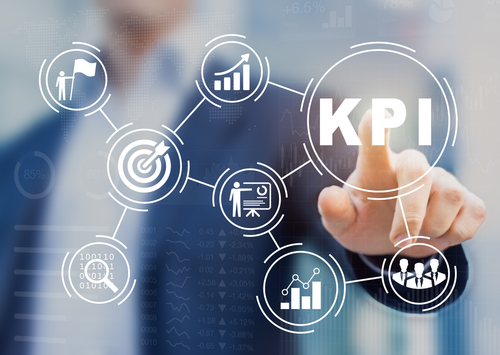
By tracking key performance indicators (KPIs) and metrics, FMs can effectively establish targets for their department, set performance measurement milestones, and gain key insights for informed decision-making. The following is a look at how facility managers can define the most important KPIs and the metrics for tracking these KPIs in their facilities.
What are KPIs?
Key performance indicators are measurable values used to check the progress of business efforts. They function like health checks for business processes and activities, and regardless of the type of business being operated, companies can use KPIs to gauge their performance over time. The concept behind KPIs is straightforward—what gets measured gets improved. The idea is to have a “yardstick” to check if a business activity or task has met the mark or fallen short.
KPIs vs. Metrics
Although KPIs and metrics are closely related, there are clear distinctions between both terms.
While KPIs are measurable values that show how effective you are at achieving specific objectives on a big-picture level, metrics show the steps for tracking specific processes.
In other words, KPIs use metrics to show where you want to go and whether you hit business objectives/targets, while metrics drill down to track specific processes that will get you where you want to go. For instance, if one of your KPIs is to reduce unplanned maintenance by 20% within six months, you would choose and track metrics that affect that KPI such as preventive maintenance compliance.
Knowing the above, the next step is deciding which KPIs are the most important for measuring performance in your premises.
Choosing and Structuring KPIs
While there is no one-size-fits-all approach for choosing FM KPIs, there are certain underlying factors that you’ll need to take into consideration every time.
In any facility, there are several ongoing processes that can impact the system, including everything from energy consumption to reactive maintenance levels, maintenance costs, etc. However, trying to track every single process will be futile and distracting. Instead, focus on those KPIs that have the most potential to deliver the desired changes as quickly as possible.
To achieve this, it’s advisable to choose KPIs that reflect the most pressing needs of your facility.
Start with the basics. Understand what your top facility maintenance objectives are and how you plan on achieving them. Consider this a fact-finding mission and approach it as an inclusive process that builds on feedback from members of your maintenance team and insights from your maintenance database. Afterward, you will gain a better understanding of which processes to prioritize with a KPI.
Also, avoid taking on too many KPIs at any one time. About four or five should do. Anything more, and you risk stretching your resources too thin (time, labor, tools, etc.). Rather, tackle one first, then as each KPI is met, you can replace it with a new one. It’s an evolving process with room for improvements.
After deciding which KPIs to track, you’ll want to structure them in a standard format to make them trackable and clear to all of your team. A popular way to do this is to present your KPIs using the SMART framework; that is, check if each KPI is:
Specific,
Measurable,
Achievable,
Relevant,
Time-frame.
Ask yourself the following:
- Is the objective specific?—Be as clear and specific as possible with what you seek to achieve. This will help you narrow down the steps necessary to achieve it.
- Can you measure progress toward that objective?—Set milestones (e.g., percentages) that will help prove your progress toward attaining your goals.
- Is the goal realistically achievable?—Set reasonable goals to keep everyone challenged yet focused.
- How relevant is the goal considering the current challenges in your organization?—Each KPI should align with an important maintenance objective.
- Is there a time-frame for achieving this goal?—Set a clear end date to boost motivation and task prioritization.
Now, let’s look at some examples of well-structured maintenance KPIs that facility managers can use today.
Some Commonly Used KPIs
Though we have established that KPIs will vary from one facility to the next, there are some commonly used KPIs and metrics that you can apply almost everywhere, such as:
- Improve Work Order Completion time by 50% over the next 12 months.
- Reduce energy consumption by 15% in eight months.
- Reduce unexpected downtime by 40% over the next 12 months.
- Reduce vehicle idle time by 20% before the end of this year.
- Achieve 95% inventory accuracy levels in seven months.
- Improve wrench time for scheduled maintenance tasks by 20% in four months.
- Reduce rework requests by 60% in six months.
Finally
Improving the activities and processes at your facility can sound difficult, considering every other task that needs your attention. But assessing your current performance through KPIs will give you an invaluable system from which to measure your progress, or lack thereof, and quickly course-correct as time passes.
Bryan Christiansen is the founder and CEO of Limble CMMS. Limble is a modern, easy-to-use mobile CMMS software designed to take the stress and chaos out of maintenance by helping managers organize, automate, and streamline their maintenance operations.