Facility teams are responsible for maintaining, inspecting, and fine-tuning a variety of equipment and facility systems, including air handlers, generators, boilers, elevators, and other equipment for safe and efficient operation.
Remembering the sizes of different belts, filters, and other applicable parts is part of the job, so facility teams rely on O&Ms (also known as equipment manuals) for these kinds of details.
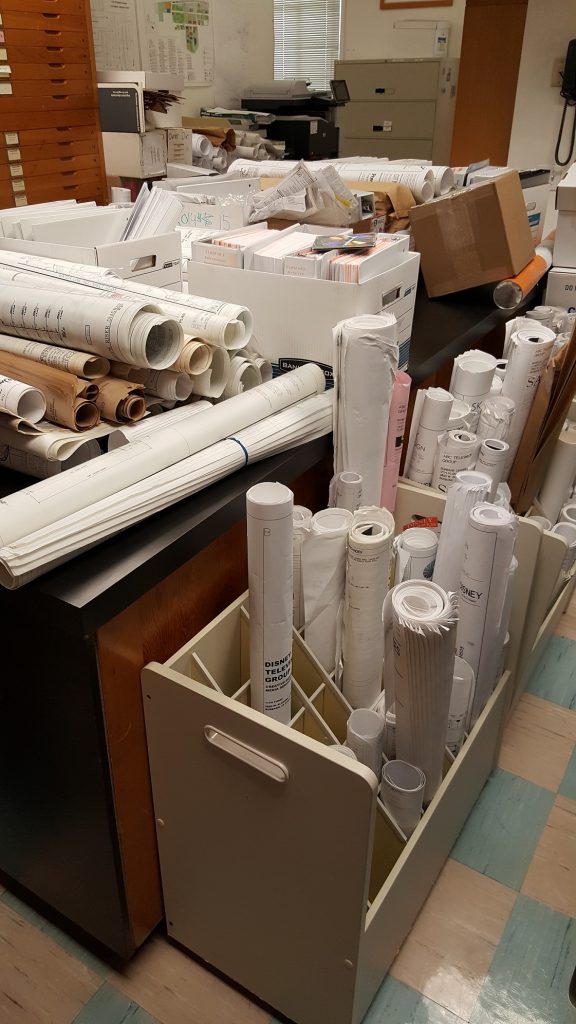
The O&M is an invaluable tool for defining the requirements and procedures for the effective operation and maintenance of equipment, based on the manufacturer’s recommendations and to keep the warranty in force.
It’s also a critical resource for facility technicians. It contains wiring details, warranty info, troubleshooting tips, info about replacing and inspecting components like filters, the make and model of parts, when bearings should be lubricated, and on and on.
When working on an HVAC system, if the airflow and proper temperature are compromised in any way, that could mean major trouble for facility managers responsible for health and safety.
Indoor air quality (IAQ) is a major post-pandemic topic. Buildings might be shut down while expensive repairs are made, which inconveniences building occupants.
Unfortunately, at many campuses the O&M manual is likely buried somewhere in the plan room of building G which is at the other end of the campus. Other times the manual is kept with the piece of equipment. In either case, being able to access that manual quickly is not likely.
Technicians are forced to rummage through numerous bookshelves, binders, and folders, until they can find the correct manual. When the manual is located, a page might be missing or illegible due to age and fading or a coffee stain!
Asking long-time employees for help with equipment maintenance, inspections, and even location of the equipment in a building has been the standard way to deal with equipment questions, especially with newer employees. Unfortunately, many Baby Boomers are retiring.
It is an ever-increasing problem that techs with 20, 30, or more years of experience are setting their eyes on retirement. And the current labor shortage makes it even more difficult to backfill their positions once they are gone.
How is that “institutional information” going to be transferred to the next mechanic or technician responsible for the job? Facilities knowledge is as much technical as it is physical or industrial. There’s always something new to learn about traditional facility equipment as well as server/network skills in some cases. Further, as equipment gets upgraded or replaced, there are new systems and skill sets to learn.
For today’s technicians, however, they need information while they’re on rooftops or basements, and time is of the essence when repairing aging or fragile equipment.
Relying on one resource for institutional knowledge just isn’t fair to newcomers; that’s why one “source of truth” is mission critical for facility teams. Further, quick and reliable access to that “source of truth” is more important than ever.
“I am a firm believer that everyone on the team should have the same access to the same current information from day one. That along, with shadowing the tenured folks, is invaluable training,” said facilities expert David Trask.
At one company, the facility team was responsible for unique and old equipment that was no longer manufactured. When the techs that serviced the equipment started to retire, team members started filming them doing the monthly, quarterly, and annual maintenance. And while doing it, they talked about where to get parts and the quirkiness of the machines. They created a shared library so the newer folks could learn from this and be quick and easy to find. Even taking this additional step, the challenge arose of “whose” computer is that stored on and what is the username/password to log in? This information is of little benefit if the recording is on a CD in the bottom of someone’s desk drawer.
Retirement/Training
As facility professionals continue to retire, the need for cross-training becomes even more dramatic.
The requirements for building engineers with technical skills has never been greater. Equipment is getting ever more sophisticated while the labor pool is becoming shallower by the month.
One technician said, “I cannot tell you how many times I have heard that former retired employees have to either change their phone number or they end up signing back on part-time because they receive so many calls after they leave.”
A lot of knowledge can be cross trained to staffs, including annual elevator inspections, building fire inspections, life safety, fire extinguisher, and boiler inspections by using checklists for tracking, implementing, and recording the successful completion of tasks.
In some cases, senior building engineers assume greater levels of responsibility and longer hours because of early retirements and a less-experienced workforce. Thinking about it in a different way, if one tech retires and is on an extended leave, how many different tasks now need to be re-assigned to others? If one small task is missed or not accounted for, it could have long-lasting negative effects.
Often, the “new guy” gets a quick training on basics and then is assigned to the night shift. That “basic” training doesn’t help at 2 a.m. when the pipe bursts and the worker can’t find the shutoff valve. As many know, incidents like that don’t care who is on shift or when.
With advances in technology like machine learning and artificial intelligence, it is now possible to extract intelligence from building information like O&Ms and make that information instantly available on mobile devices, which everyone uses.
It just doesn’t make sense in 2021 to rely on plan room visits, paper documents, or our memories to keep facility equipment up and running.
When everyone on the team has the same access to the same current information from day one, then everyone benefits.
Jack Rubinger is marketing content writer for ARC Facilities. He can be reached at jack.rubinger@arcfacilities.com