Facilities managers know the importance of maintaining proper indoor air quality (IAQ). As far as critical issues go, air quality, ventilation, and the prevention of pollutants are up there, as they pose a severe health risk to workers, not to mention productivity and efficiency.
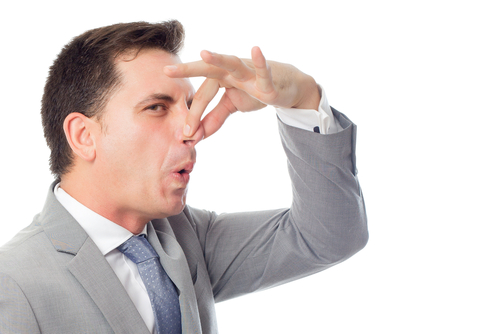
One of the most prevalent indoor air contaminants is volatile organic compounds (VOCs), which can be emitted by numerous sources likely to be present in any indoor facility. Furthermore, while sources may vary, the emission of odors can also have a profound impact on worker health and productivity, which is why proper control and caution should be maintained to prevent these from materializing. Oftentimes, the source of VOCs and odors can be the same.
This article discusses the strategies that facilities managers can implement to monitor, control, and improve air quality by minimizing VOCs and reducing odors in commercial environments.
Understanding VOCs and Odors in Office Environments
VOCs are emitted by many indoor sources like lead paints, adhesives, cleaning agents, and even carpets, among others. Odors arise most commonly from sources such as waste bins, food preparation areas, restrooms, exhausts, building materials, and so on.
When inhaled, VOCs can cause headaches, drowsiness, irritation, and other issues after prolonged exposure. Many naturally emit strong scents and odors, which some individuals may be particularly sensitive to. Over time, exposure to the smells emitted from these materials has a knock-on effect on workplace comfort and satisfaction and may hinder an employee’s ability to complete tasks.
Facilities managers should be aware of common VOC and odor trouble spots:
- Construction or renovation projects where glues, paints, and adhesives are likely to be present
- Recent furnishings or carpet installations
- Office equipment like printers and photocopiers
- Cafeterias and breakrooms
- Bathrooms
- Garbage collection areas
- Nearby vehicle activity, particularly if exhaust fumes can enter through ventilation pipes
Periodically surveying the facility to detect VOC or odor issues early is strongly advised. Whether this is conducted internally or with the help of an outsourced professional, enlisting this type of assistance is the first step in identifying problem areas and the appropriate remedial action.
Monitoring and Assessing Indoor Air Quality
To effectively manage VOCs and odors, facilities managers should install systems and monitoring solutions that check and dispel data about IAQ in real time.
This starts with the following approaches:
- Conduct walk-through assessments: Make note of any prominent odor locations, visually inspect the areas for pollution sources, and regularly speak with employees about any notable concerns.
- Measure VOC levels: Use devices like photoionization detectors (PIDs), flame ionization detectors (FIDs), or metal oxide semiconductor sensors (MOSs) to measure VOCs in the air accurately.
- Carry out ventilation checks: Ensure any HVAC or air conditioning systems are calibrated properly to provide adequate fresh air to all occupied areas, as per the ASHRAE Standards 62.1 and 62.2.
- Trend monitoring: Keep long-term indoor air quality records to identify patterns and improvements.
Mitigating VOCs and Odors Through Ventilation
Diluting the presence of VOCs and odors boils down to optimizing the amount of fresh air and ventilation that your facility receives.
Consider increasing the total airflow levels within your facility and installing CO2 sensors for demand-controlled ventilation. This will help your facility’s ventilation rate match up to the real-time occupancy of your building, ensuring that all inhabitants are getting sufficient fresh air regardless of how busy it is. Compact spaces may require more strategic methods of fresh air provision.
In addition, ensure that you check for ventilation deficiencies like:
- Leaking or blocked ducts
- Blocked or noisy filters
- Sensors needing calibration
- Supply vents or coils improperly placed
Make sure to invest in proper maintenance of all essential HVAC components to sustain optimal performance year-round. Make sure that equipment is kept running, even during off-hours, to ensure sufficient airflow. You may wish to invest in long-term planned preventative maintenance contracts from your HVAC installer to keep costs to a minimum, with monthly fees covering costs of repairs, replacements, and maintenance checks.
Advanced Air Purification Solutions
Where ventilation alone is insufficient to control VOCs or smells entirely, specialized air cleaning systems should be installed where appropriate. Depending on your facility and the nature of materials that you are keeping on-site, you may need to consider installing certain technologies that can provide additional control and abatement.
Technologies to consider include:
- Industrial-grade carbon filters: Portable, turnkey, industrial-grade carbon filters provide complex odor entrapment and VOC absorption in a variety of sectors and institutions.
- Photocatalytic oxidation (PCO): This process oxidizes odor-emitting pollutants and contaminants using a mixture of ultraviolet lights and titanium dioxide catalysts. In other words, it removes the chemicals from VOCs, for example, into harmless water and carbon dioxide.
- Negative ion generators: Also known as air ionizers, these emit negative ions or charged atoms that attach to particles in the air, such as those in tobacco smoke, mold, or hazardous chemicals. The ions combine and clump together before precipitating.
These are just some examples of remediation technologies that can purify acrid air that grows in intensity when near pollutant sources.
Maintaining Good IAQ Practices
Technology aside, facilities managers can implement strict administrative policies and measures to minimize the presence of odors and VOCs for the benefit of their staff.
For instance:
- Choose low- or zero-VOC materials, adhesives, and solutions.
- Install local exhaust ventilation systems in rooms where scents and smells are likely to be most prominent.
- Prohibit odorous foods from entering the premises.
- Ensure sufficient and adequate storage of chemicals in designated areas with clear signage.
- Schedule cleaning, trash removal, deliveries, and other odor-emitting activities during periods of low or zero occupancy.
- Ban indoor smoking and vaping.
- Educate employees on the dangers and hazards of improper IAQ and insufficient maintenance, and solicit regular feedback for continuous improvement.
By being vigilant through monitoring, assessing, and troubleshooting, facilities managers can take a proactive stance to provide workplaces with clean, breathable air.
Chester Avey has over a decade of experience in business growth management and cybersecurity. He enjoys sharing his knowledge with other like-minded professionals through his writing. You can connect with Chester by following him on Twitter @ChesterAvey