Between extreme weather events, an aging power grid, and the transition to renewable energy, power interruptions are becoming a much greater risk in all parts of the country.
Many will remember the highly publicized 2013 Super Bowl blackout when the power shut down the biggest game in American sports for 34 minutes, plunging the New Orleans Superdome into darkness. When the lights, escalators, and credit card machines stopped working, fans were inconvenienced, but fortunately not at serious risk.
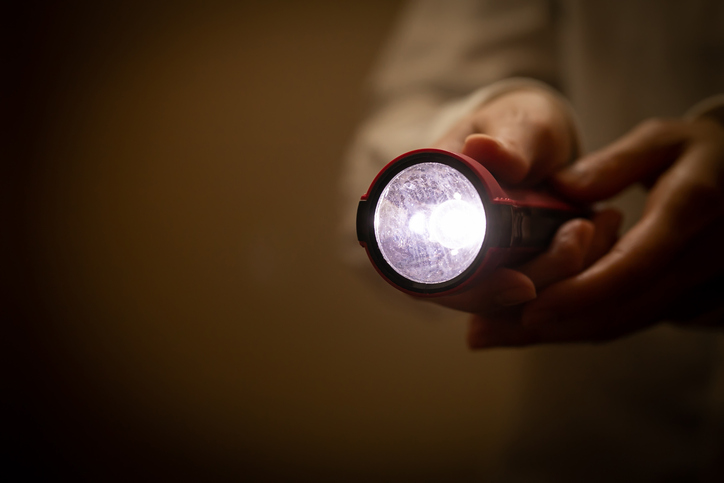
That’s hardly the case in industrial and manufacturing facilities, where “lights out” can put lives in danger. The Occupational Safety and Health Administration (OSHA) has already identified poor lighting as a leading cause of injuries caused by slips, trips, falls, and contact with objects and equipment. Amid heavy machinery, moving equipment, and sometimes already hazardous conditions, power failures pose even greater risks to workers on a daily basis.
Production disruptions and equipment damage caused by outages or unstable power can dramatically increase operating expenses and cut into revenue and profitability. With the cost of unplanned downtime as high as $22,000 per minute and totaling $50 billion a year in manufacturing, no company can afford to deal with unplanned power interruptions.
Make Safety Priority No. 1 with Failure-Resistant Lighting
Adding to those financial impacts, the cost of accidents, injuries, and lost time due to safety hazards can accumulate quickly.
In many facilities, extreme conditions like dust, debris, high temperature, and vibration can wreak havoc on lighting, causing unexpected fixture failure, dark shadows, and overall poor visibility. In the event of even a brief power loss, antiquated fixtures can take up to 20 minutes to come back to full brightness, creating an unnecessary safety risk.
It is essential that workers have adequate lighting at all times, and studies show that simply improving facility lighting can reduce workplace accidents by as much as 60%. Industrial light-emitting diode (LED) lighting offers crisp, near-daylight illumination that provides more natural color rendering to help workers identify hazards and eliminates the need for supplemental lighting like flashlights. It also provides for a quick re-strike to restore visibility instantly when power is restored. And, because LED lights use at least 75% less electricity than conventional fixtures, they can run more efficiently on battery or backup generator power, which means longer run time and more lights in operation at once.
Some LED fixtures provide self-testing and automated diagnostics, which eliminates the need for periodic push-button tests to ensure functionality. Fixtures with indicator lights make visual inspection easy, while automated weekly and yearly testing offers peace of mind, ensuring built-in fixture batteries are charged and operating properly at all times.
Have a Power Plan
Aside from installing more modern lighting and backup generators, having a power failure and restoration plan in place can dramatically reduce the risk of accidents and injury, minimize downtime, and ensure a quick, smooth return to operations.
Here are three ways to proactively mitigate the impact of power outages:
1. Develop and implement robust power failure procedures. Create a formal power failure procedure that outlines critical equipment identification, emergency power sources, and shutting down non-essential systems. Run frequent scenario response tests and emergency drills to refine the plan, and review and update procedures based on practice outcomes and real-world events to ensure adaptability to new equipment and operational challenges.
2. Periodically upgrade equipment. Consider installing updated light fixtures with built-in battery backup to ensure bright, safe illumination in the event of power failure. Choose lighting fixtures containing surge protectors and voltage regulators to safeguard critical components and minimize potential damage during instances of power instability or failure. Install emergency back-up generators to run critical safety and operation checks to keep workers safe and production going as much as possible.
3. Prioritize quality when investing in facility and exit lighting fixtures. Ensure these fixtures are designed to withstand the challenges of industrial environments, including high heat, vibration, debris, unstable power conditions, and potentially explosive atmospheres. It’s essential to choose fixtures that meet the required hazardous location certifications, including internal flame paths to prevent sparks from escaping, keeping your employees and facilities safe. Lastly, focus on lighting manufacturers that conduct a variety of premarket testing, such as Accelerated Life Testing (ALT), to ensure that the fixtures will perform as advertised over the long haul even in challenging industrial environments.
Power failures don’t have to be a risk to your employees, equipment, or profitability. With the right solutions, a preparedness plan, and some best practices, your facility can weather any storm and be future-ready with resilient, efficient systems that address today’s needs and tomorrow’s challenges.
Rizwan Ahmad is vice president of product development and management at LED industrial lighting company Dialight.
ALSO READ: Maintenance Tips for Your Facility’s Backup Power Generator