The U.S. Environmental Protection Agency (EPA) has announced that 86 U.S. manufacturing plants earned the agency’s ENERGY STAR certification in 2022, a designation reserved for manufacturing plants in the top 25% of energy efficiency in their sector.
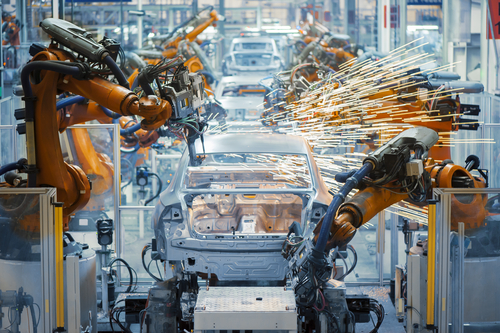
Together, these plants saved over 105 trillion British thermal units (Btus) of energy and prevented more than 6 million metric tons of carbon dioxide emissions, equivalent to the emissions from the electricity use of more than 1.1 million American homes.
“Industrial leadership in energy efficiency is critical to achieving our nation’s climate goals,” said EPA Administrator Michael S. Regan. “The savings from ENERGY STAR-certified plants demonstrate how energy efficiency is both helping our manufacturing sector reduce costs and propelling America’s transition to a clean energy future.”
The industrial sector accounts for 30% of U.S. greenhouse gas emissions, primarily from energy use in manufacturing plants. ENERGY STAR-certified plants have reduced their energy consumption through a variety of energy efficiency projects and management practices. For example:
- Primient’s Loudon, Tenn., and Lafayette, Ind., wet corn mills reduced their CO2e emissions by installing and optimizing combined heat and power systems.
- Ash Grove’s Seattle, Wash., cement plant automated the support equipment in their grinding mills to cease operation when the mills do.
- Astra Zeneca’s Newark, Del., pharmaceutical plant installed a heat recovery system that reduced natural gas usage by approximately 20% and a heat exchanger that provides free chilled water during winter months.
- General Motors’ Fort Wayne, Ind., auto assembly plant recovered waste heat from the engine jackets and exhausts ducts of its landfill gas cogeneration units, reducing the plant’s winter natural gas consumption. Additionally, the company’s Flint, Mich., assembly plant updated more than 90% of its lighting, installed light emitting diodes (LEDs) with motion sensors to decrease light levels after a period of inactivity, and continued to focus on reducing energy during non-production periods.
ALSO READ: Back to Basics: How Businesses Can Participate in the ENERGY STAR Program
- Nissan North America’s Canton, Miss., vehicle assembly plant formed a team to track compressed air leaks, leading to an annual reduction of approximately 1,700 cubic feet per minute of compressed air. The company’s Decherd, Tenn., powertrain assembly plant created scorecards to benchmark the shutdown performance of facilities, assigned countermeasures to shops not meeting targets, and provided recognition to top performers.
- Titan America’s Troutville, Va., and Medley, Fla., cement plants have completely converted production to Portland Limestone (Type IL) cement, with up to 15% less embodied carbon than standard Portland Cement. Since 2015 the two plants also have achieved a 12% reduction in electricity use and an 18% reduction in CO2, respectively, from improved energy management.
- Cemex’s Miami, Fla., cement plant increased its energy performance in 2022 by modifying a finish mill, optimizing the ball charge on the largest mill, and identifying and correcting potential energy losses while also increasing the production of Portland Limestone (Type IL) cement.
Manufacturing plants use EPA’s ENERGY STAR energy performance indicators—or, in the case of petroleum refineries, the Solomon Associates Energy Intensity Index scoring system—to assess their energy performance. Plants that score a 75 out of 100 or higher, indicating they are more energy efficient than 75% of similar facilities nationwide, are eligible to earn ENERGY STAR certification. ENERGY STAR certification is available for 20 manufacturing sectors, from cement and steel to glass and commercial bakeries.
The full list of ENERGY STAR-certified plants for 2022 is available here.