June is National Safety Month, making this the perfect time for facilities managers to better understand safety signs. We’re talking about those signs, also known as “warning” or “hazard” signs, placed on floors to warn people to be careful that there may be a hazard ahead.
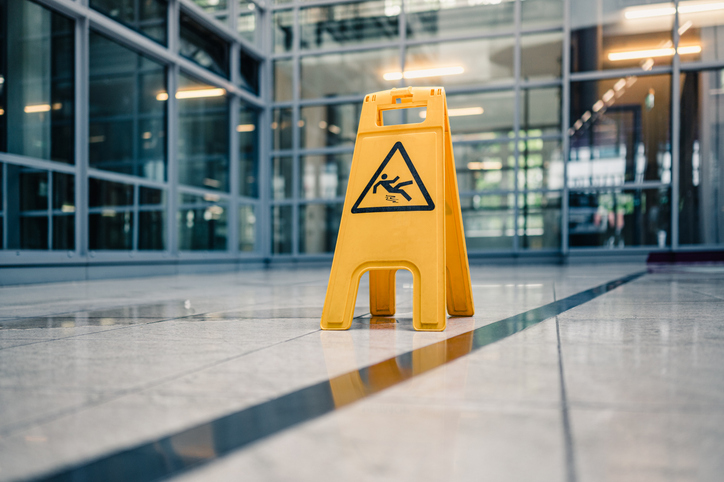
These signs are typically placed when floor maintenance is being performed, but they also serve as a warning when there are spills, grease, oil, or other contaminants on the floor. They’re also used to prevent slips-and-falls when cords are crossing the floor, when there’s damage to the floor surface, or at transition areas, which could lead to a trip-and-fall accident.
It’s important for facilities managers to note that the words used on these signs carry different implications. Let’s take a closer look:
Hazard may be present: Imagine a scenario where maintenance workers are changing lightbulbs in an interior walkway. In this case, a hazard sign with the word “caution” should be prominently displayed, indicating the potential for an accident or injury.
Hazard possible but not probable: A more urgent message would indicate the possibility but not necessarily the probability of an injury or death if continuing in the risk area. In such a case, the word “warning” is printed on the sign.
Hazard high probability: This is the most urgent of the three types of safety signs discussed here. The word “danger” would be boldly written, usually in red, on these signs. Danger signs should be used only in extreme situations when people could very likely be harmed if they continue walking through an area.
Other words used on safety signs include “notice,” which might be used, for instance, to tell facility occupants to use the handrail when walking on stairs. “Emergency” is used to indicate procedural instructions such as “emergency exit” or “emergency eye bath.”
Tips on Selecting Safety Signs
Choosing safety signs is a task that should not be underestimated. It’s a complex process that goes beyond simply understanding the words on a sign. It is recommended, if not essential, that facilities managers seek assistance from their local independent distributor to navigate this complexity.
Local distributors do much more than sell products to facilities managers. Especially if they are part of a distributor membership organization, they are taught to educate managers on how to make their facilities cleaner, healthier, and safer, including how to select safety signs.
For instance, they would likely suggest the following:
- Signs should be highly visible; yellow signs are often the most visible and, because of this, are used universally.
- In North America, they should be written in English and Spanish.
- Look for durable signs that are also stackable, taking up less space in closets.
- Use the proper sign for each specific reason—for instance, if the floor ahead is wet, a sign indicating “wet floor” should be selected.
- Signs should have UV protection so they can be used outside.
- They should be three-sided, making them less likely to fall.
- Height should be 25 to 35 inches.
Safety Sign Placement
One thing more we must discuss is safety sign placement. Once again, it can be more complex than initially realized. For instance:
- According to OSHA, safety signs should be placed as close to the relevant hazard as possible.
- Signs should outline the risk area. This sets safety parameters so walkers know where they can and should not walk.
- Signs should be removed once the risk has been eliminated.
This last point is critical. Safety and warning signs lose their impact and meaning to building occupants if they are left after a danger has passed. What happens is that people come to ignore the safety signs, which is one of the worst things a facilities manager or their maintenance crew wants to happen.
Not Just for June
While June is National Safety Month, the importance of building safety extends far beyond a single month. It’s a year-round, everyday concern for facilities managers. As they strive to maintain clean, healthy, and safe properties, the proper selection and use of safety signs plays a vital role in achieving this goal.
Michael Wilson is the CEO of AFFLINK, a distributor membership organization made up of nearly 300 distributors in North America. He has been with the organization since 2006 and provides strategic leadership for distributor members around the country. In his free time, Michael works with the Wounded Warrior Project, helping veterans heal and get their lives back on track. He can be reached through his company website at www.afflink.com.