In the dynamic world of facilities management, where the challenge lies in maintaining peak operational conditions amidst budget constraints, the adage “an ounce of prevention is worth a pound of cure” becomes more than just a saying—it’s a necessity. As organizations strive for efficiency with limited resources, embracing a robust preventive maintenance program emerges as a crucial strategy.
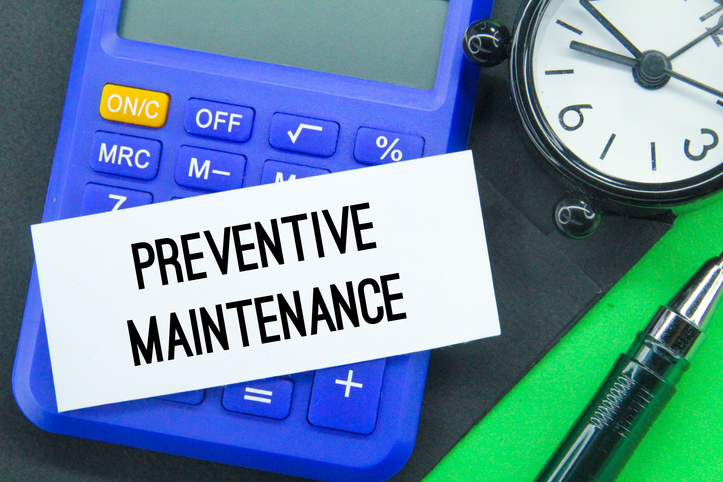
The heart of the matter lies in proactively addressing potential problems rather than reacting to them. Instead of waiting for equipment malfunctions, which disrupt operations and result in costly emergency repairs, preventive maintenance enables facilities managers to identify and rectify issues before they escalate. According to research from Brightly, a Siemens company, this proactive approach can reduce costs by 12%-18% and deliver an outstanding 400% return on investment (ROI).
The essence lies in understanding the nuanced advantages of preventive maintenance—from concrete financial savings to the intangible yet impactful realms of increased productivity and streamlined operations. Let’s dive into it.
6 Benefits of Preventive Maintenance
1. Minimizing Asset Downtime for Increased ROI
Preventive maintenance is pivotal in minimizing asset downtime, contributing to increased maintenance ROI, by proactively addressing potential issues before they escalate into disruptive failures. Adhering to a regular schedule of inspections, calibrations, and maintenance tasks enables facilities to identify and correct problems early, preventing unexpected breakdowns and downtime.
2. Increasing Sustainability Through Efficiency
Emphasizing increased energy efficiency, lower utility costs, and a commitment to environmental stewardship, preventive maintenance aligns with sustainability goals. Well-maintained assets not only live longer and run more efficiently, but also contribute to a greener operation by using fewer resources.
3. Reducing Major Repairs for Enhanced Reliability
A well-structured preventive maintenance plan protects against unexpected asset failure by systematically addressing potential vulnerabilities. Regular inspections, servicing, and upkeep detect and rectify emerging issues, minimizing the risk of unexpected failures and reducing the need for unplanned, resource-intensive repairs.
4. Extending Asset Life Through Proactive Care
Regular inspections, lubrication, calibration, and timely replacements are key elements in maintaining equipment health, reducing stress on components, and minimizing the risk of premature failure. Studies have shown that proper preventive maintenance can extend an asset’s lifecycle significantly. Without preventive maintenance, a rule of thumb suggests anticipating a 20% loss in asset life, where the cost to replace the asset early far exceeds the cost of preventive maintenance.
5. Increasing Productivity Through Uninterrupted Operations
Minimizing disruptions caused by unexpected breakdowns and repairs translates to consistent asset performance, reduced maintenance cost, and lower total cost of ownership. Preventive maintenance fosters a culture of proactive problem-solving and continuous improvement, leading to enhanced operational efficiency. The image of a maintenance team is crucial—if there are repeated problems, people will blame those who are responsible for maintaining it. A smoothly running facility rarely notices their presence, showcasing the team’s effectiveness.
6. Cost Reduction Through Avoidance of Reactive Maintenance Expenses
The costs associated with reactive maintenance—including urgent repairs, overtime, rush orders, and potential major repairs or equipment replacement—can accumulate rapidly and amount to nearly four times that of preventive maintenance. A proactive preventive maintenance approach mitigates financial strain, fostering a more efficient, reliable, and sustainable maintenance strategy. This not only saves immediate costs, but also contributes to enhanced efficiency, workflow continuity, and long-term operational success.
A Mandate for Sustained Success
As organizations navigate the complex landscape of facilities management, understanding and embracing the strategic value of preventive maintenance is not just a choice—it’s a mandate for sustained success. From financial savings to operational efficiency, the benefits are real, tangible, and transformative. It’s time to view preventive maintenance not as an expense line, but as a strategic investment that propels facilities management into a realm of enhanced productivity, reliability, and long-term success.
Luke Anderson, FMP, is a strategic solutions consultant at Brightly, a Siemens company. He focuses on the public sector and has been in the industry since 2012, both on the construction side and in asset management consulting.