With the Labor Day holiday officially in the books, not only is back-to-school season in full swing, but the return-to-office (RTO) is underway, as well. Over the past few years, the late summer and early autumn have marked a rallying point for companies’ RTO efforts. While Zoom’s recently revamped RTO policies have been grabbing the headlines in recent weeks, last summer it was Apple announcing its plans for a post-summer return, and before that, Google rolled out a similar game plan in 2021.
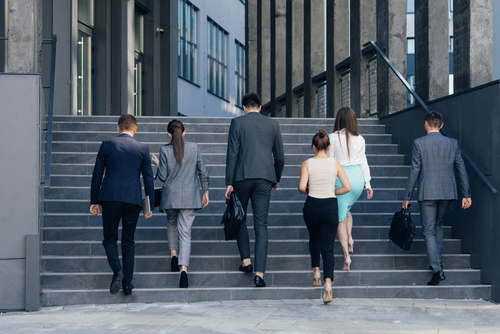
The majority of these plans for bringing employees back to the office involve more flexibility than the working accommodations of the pre-pandemic landscape. For example, Zoom’s new policy is more of a structured hybrid approach where employees are on-site two days out of the week.
While RTO in policy can be different from RTO in practice, the latest data suggests that the office surge is in full effect. According to the results of Eptura’s Q2 Workplace Index Report, the Americas (84%), Asia-Pacific (83%), and Europe, the Middle East, and Africa (70%) regions all saw significant year-over-year increases in desk bookings. Room bookings, an indicator of broader in-person team collaboration, also increased year-over-year in each region in the Americas (48%), APAC (67%), and EMEA (57%) regions.
The data shows that more employees are returning to the office and with more freedom to choose how, and where, they want to work. As companies experience these surges in occupancy and attempt to plan the future of their workspaces, businesses find themselves with a new set of considerations, particularly as it relates to facility maintenance and its corresponding impact on carbon emissions.
Connecting the Dots Between Maintenance and Emissions
In addition to juggling all of the decisions around bringing employees back to the office, today’s business leaders are under immense pressure—whether it be from regulatory bodies, corporate commitments, or otherwise—to reduce their CO2 emissions. With buildings accounting for 39% of global carbon emissions, much of that burden ends up falling back on the shoulders of facility management and maintenance personnel.
Responsible for the day-to-day operations of facilities that are experiencing spikes in occupancy from RTO, these teams have an opportunity to reduce carbon emissions by adjusting their current maintenance strategies. Small adjustments in response to corrective maintenance and in preparation for preventive maintenance can accumulate for a significant impact to a facility’s emissions totals.
Changing the Strategy
While the ideal ratio of preventive to corrective maintenance is 4:1, data from the latest Workplace Index shows that organizations are operating at a ratio of 4:7. This means that for every four work orders planned, maintenance teams are responding to more than seven break-fix or other ad hoc ticket requests.
By readjusting existing maintenance strategies, organizations can shift the balance of maintenance activities from unscheduled to scheduled, optimizing the work based on real trends in building occupancy to better meet sustainability targets. There are several components for organizations to consider as they assess their strategies and readjust to better meet the needs of their current workplaces.
Managing Assets and Making Smarter Decisions
The emergence of intelligent asset management software can provide added visibility and context to a business’ carbon emissions in the era of flexible working arrangements. A robust asset management program can offer cost-effective ways for businesses to scale back their emissions and better facilitate building maintenance.
At the foundation of smarter maintenance decisions is understanding and mapping workplace usage. With improved access to comprehensive facility data, companies can now measure desk usage and occupancy levels and use this information to determine where potential energy savings can be made. RTO means that workspaces are, in many cases, returning to pre-pandemic levels of usage on certain days of the week.
Facility teams must be prepared to adapt to these fluctuations, understanding which spaces will be highly trafficked and when. This enables businesses to reduce energy use in certain areas during quiet periods, prioritize work orders and preventive maintenance in high-traffic spaces, and more. All of these tactics can help businesses demonstrate what they are doing to meet sustainability goals.
Additionally, asset management enables facility teams to proactively track equipment wear and tear, extending the lifetime value of assets and ensuring efficient use over time. From traditional office assets, like computers and printers, to larger building infrastructure, like HVAC systems, each item plays a role in an organization’s broader carbon footprint. With insights into the usage, performance, and status of each of these assets, facility teams can make smarter replacement and upgrade decisions to drive efficiency throughout their spaces.
A Path to Progress
Widespread RTO efforts are an adjustment for everyone from executives to managers to individual contributors. Facility and maintenance teams find themselves in a unique position where RTO serves as a benchmark to evaluate the processes and procedures they have in place.
Asset management plays a crucial role in ensuring that organizations are sufficiently equipped for RTO and tracking toward company-wide sustainability objectives. With a deeper understanding of how workspaces and assets are being used, facility teams can begin to prioritize preventive maintenance over reactive maintenance. In doing so, companies can make a series of marginal, day-to-day gains, all amounting to a significant reduction in carbon emissions.
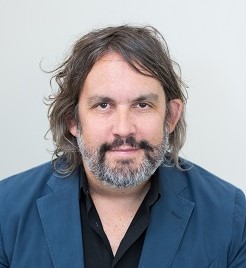
Paul Phillips is the chief technology officer at global worktech company Eptura.