Artificial intelligence (AI) has very quickly become familiar to everyone involved in facilities management. Through prescriptive data insights, combining advanced analytics and AI-driven recommendations, there are a wealth of benefits that AI brings for the industry. After all, McKinsey research estimates that generative AI could soon make up $4.4 trillion of value annually.

The rise of intelligent buildings, driven by innovative installations and building information modeling (BIM), has revolutionized cost reduction, project timelines, and information exchange among stakeholders. AI is undoubtedly set to remain a dominant force in this evolution. However, while it is tempting to view AI as a universal solution capable of addressing all challenges, its implementation comes with critical considerations. The focus often overlooks the prerequisites for effectively leveraging AI and the potential threat it poses to human jobs if not deployed responsibly and thoughtfully.
The role of a facilities manager is evolving very quickly, leading to an increasing skills gap. With AI becoming commonplace, workers must understand both legacy mechanical plant systems in old buildings and building automation systems in modern buildings. The key is upskilling employees to have an AI-literate workforce that can perform predictive maintenance functions without jeopardizing their own positions. Let’s discuss how the industry can strike this balance.
The Predictive Maintenance Benefits
Firstly, it’s worth outlining how predictive maintenance can continue to have a positive effect on facilities management operations. Preventive and predictive maintenance remain priorities, with 29% of survey respondents from a report on “A Facility Manager’s Guide to Building a Relationship with AI” emphasizing the importance of automated scheduling and insights.
If you take an HVAC system, for example, AI can be used to analyze real-time data that might indicate a fault or temperature change within the system so that settings can be adjusted and optimal performance and energy efficiency are achieved. On top of that, AI-driven predictive maintenance minimizes downtime and extends the lifespan of equipment, leading to further cost savings.
The Employment Challenge
A report from JLL highlights that there is an increasing reliance on automation and AI to cope with workloads in spite of ever-tightening budgets—75% of facilities managers cite budgetary constraints as their No. 1 challenge. So, despite the clear benefits that we discussed, about 60% of managers lack a clearly defined AI strategy when it comes to predictive maintenance, meaning there is a clear gap between the interest in the technology and the ability to implement it.
The industry also has to deal with the sheer number of retiring workers, and this is where the improvement in trade schools can be significant. They need to focus on educating new workers on strategic and value-added tasks that AI cannot solve. Knowing how to look at a data set and use those insights for optimized delivery is a key human capability in facilities management. This will ensure that, as AI continues to mature, it keeps complementing human skills rather than replacing them.
Change Management and Collaboration
Part of the process of pivoting to the use of predictive maintenance is learning how to effectively manage this change so that the transition is smooth and that workers do not feel undermined. This is where the concept of change management is essential to stop any resistance to the technology while maintaining productivity. Employee training is vital here, especially in the context of AI and predictive maintenance.
Maintenance teams are often used to schedule maintenance routines, so the idea of potentially deviating from that with a predictive model requires a mindset shift, trust in AI recommendations, and new skills in data interpretation. Employees need to be offered training on how to interpret predictive maintenance outputs and ideally be supported by one particular technician who can be the “change agent” and is passionate about predictive maintenance and wants to champion this new system.
Finally, it’s important to have a clear timeframe with achievable milestones for predictive maintenance adoption. That way, you can ease it in rather than overburden staff, and it’s a good idea to utilize it on non-critical assets, too.
Overall, predictive maintenance represents a huge step forward in facilities management, given its benefits related to cost savings and extended equipment lifespan. However, how well it is adopted depends on balancing its capabilities with human talent, so prioritizing employee upskilling while creating a clear structure for the change will ensure that predictive maintenance complements the current workforce.
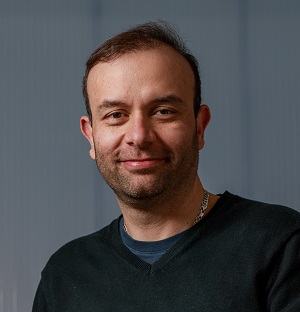
Christian Struve is co-founder and CEO of Fracttal, a provider of maintenance management solutions.