Continuous improvement in manufacturing refers to ongoing efforts to enhance products, services, or processes. The improvements can be incremental over time or achieved through breakthrough moments. However, the goal is to streamline operations, reduce waste, and increase efficiency and productivity in manufacturing facilities.
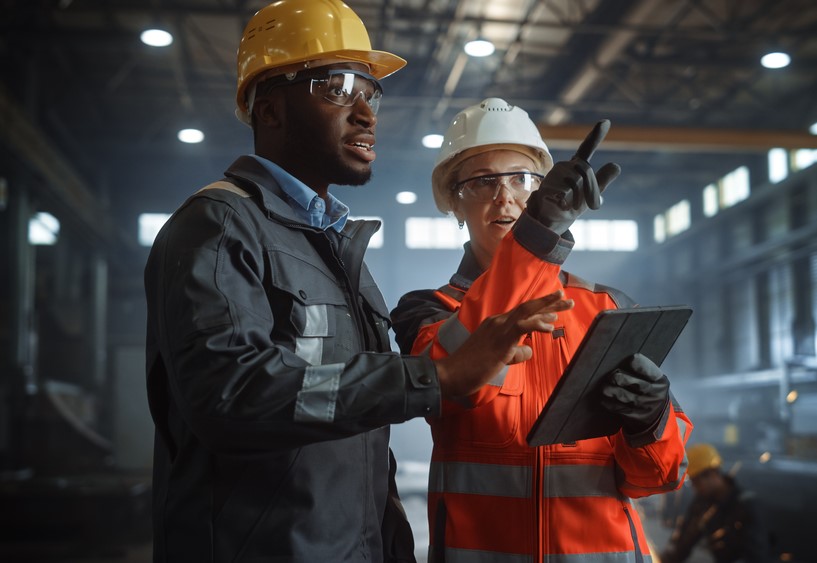
Embedding a culture of continuous development and refinement in manufacturing facilities is crucial for sustained success. This culture encourages employees at all levels to continuously seek ways to improve their work. It leads to improved operational efficiency while fostering innovation and adaptability in a rapidly evolving industry.
Establishing Effective Communication Channels
Facilities managers and plant managers play a key role in establishing effective communication channels in manufacturing environments. Strong communication ensures that goals, strategies, and feedback flow seamlessly across different levels. It is essential for aligning the workforce towards common objectives and ensuring operational efficiency.
Transparent and timely communication in manufacturing facilities can be achieved through various strategies. Regular meetings, open forums, and digital communication platforms enable a flow of information. These methods help in clarifying objectives, addressing concerns, and fostering a collaborative work environment.
Fostering Employee Engagement
Employee engagement is a driving force in the continuous improvement of manufacturing facilities. Engaged employees are more likely to contribute ideas, show commitment to quality, and strive for excellence. Their involvement is a critical factor in driving innovation and operational improvements.
Maintenance teams and engineers can encourage employee involvement through recognition programs, collaborative project teams, and open suggestion schemes. Providing opportunities for employees to voice their ideas and participate in problem-solving fosters a sense of ownership and commitment. This involvement is instrumental in driving continuous improvement.
Engaged employees significantly impact innovation and efficiency in manufacturing facilities. Their enthusiasm and commitment lead to creative solutions and process optimizations. Such a workforce is a key asset in maintaining a competitive edge and adapting to market changes.
Utilizing Data-Driven Decision-Making
For supply chain managers and manufacturing executives, data-driven decision-making is essential. Data helps manufacturers identify trends, predict outcomes, and make informed decisions. It enhances operational efficiency and helps in achieving strategic objectives.
Integrating data analytics into operational strategies in manufacturing leads to more informed and effective decision-making. Analyzing performance data helps manufacturers identify areas for improvement, optimize processes, and predict future trends. This approach is essential for achieving operational excellence and staying ahead of the competition.
Data-driven successes in manufacturing are numerous and varied. Companies have used data analytics to reduce downtime, optimize supply chains, and improve product quality. These successes demonstrate the power of data in driving efficiency, reducing costs, and enhancing customer satisfaction.
Embracing Technological Advancements
Identifying relevant technologies for manufacturing facilities is a critical step toward modernization. Technologies such as the Internet of Things (IoT), artificial intelligence (AI), and robotics offer opportunities for automation, improved accuracy, and enhanced productivity. Selecting the right technologies that align with specific operational needs is key to gaining maximum benefits.
Connected manufacturing is a key example in this respect. By integrating various digital technologies like IoT, AI, and machine learning, connected manufacturing can optimize production processes, improve data accuracy, and enhance overall operational efficiency.
Technology providers play a significant role in the modernization of manufacturing facilities. They offer not only advanced tools and systems but also expertise and support. Their involvement is crucial in ensuring the seamless integration of new technologies with existing processes.
Aligning technological upgrades with traditional processes is vital for smooth transitions in manufacturing facilities. While embracing new technologies is important, it’s equally crucial to ensure they complement and enhance existing processes. A balanced approach leads to improved efficiency without disrupting the core operations.
Continuous Training and Education
Continuous training and education are essential for improving manufacturing facilities. As technologies and processes evolve, equipping employees with new skills and knowledge is crucial. This ongoing development ensures that the workforce remains competent and adaptive to changes.
Developing strategies for ongoing training for engineers, maintenance teams, and managers involves a mix of formal education, on-the-job training, and workshops. Emphasizing skill development and knowledge sharing ensures that the team is well-equipped to handle new challenges and technologies. These strategies are integral in maintaining a high-performing and versatile workforce.
Consultants and advisors provide valuable external expertise in continuous training and education. Their insights and specialized knowledge can help in identifying skill gaps, designing training programs, and introducing best practices. Their role is pivotal in enhancing the capabilities of the workforce and driving organizational growth.
Addressing Challenges and Obstacles
Continuous improvement in manufacturing often encounters specific challenges that can impede progress. Recognizing these barriers and implementing effective solutions is crucial for maintaining momentum and fostering innovation. Here’s a list of common challenges paired with their respective solutions:
- Resistance to change: This often stems from uncertainty or comfort with the status quo. Engage employees in the change process through clear communication, involve them in decision-making, and demonstrate the benefits of new approaches.
- Limited resources: Constraints such as budget, time, or manpower can restrict improvement initiatives. Optimize resource allocation by prioritizing projects, seeking cost-effective solutions, and leveraging existing assets more efficiently.
- Lack of clear strategy: Without a well-defined direction, efforts can become unfocused and ineffective. Develop a clear and concise strategic plan that outlines objectives, timelines, and expected outcomes, ensuring alignment with the overall goals of the organization.
- Inadequate leadership: Poor leadership can lead to a lack of direction and motivation among employees. Foster strong leadership by training managers and leaders in effective communication, problem-solving, and motivational techniques.
- Insufficient employee engagement: Low engagement can lead to a lack of innovative ideas and reduced productivity. Foster a culture of openness and flexibility, recognize and reward contributions, and involve employees in decision-making processes.
- Technological limitations: Outdated technology can hinder efficiency and innovation. Identify and invest in relevant technologies that enhance operations, and provide training for employees to effectively utilize these tools.
Addressing each of these challenges with targeted solutions will enable manufacturing facilities to continue improving and innovating effectively. This approach not only overcomes obstacles but also creates an environment conducive to continuous growth and development.
Conclusion
Continuously improving operations, embracing change, and investing in people and technologies helps manufacturers stay competitive and responsive to market demands. These efforts lead to long-term success and a strong position in the industry.
And the industry is evolving rapidly, driven by technological advancements and changing market dynamics. In this environment, continuous improvement is not just beneficial, but essential. It enables manufacturers to adapt, innovate, and excel, ensuring their relevance and success in a constantly changing landscape.
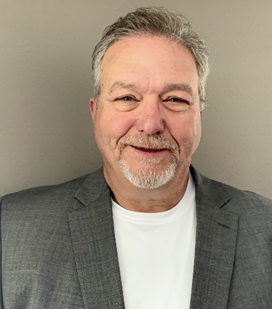
With over 30 years of experience in the manufacturing space, Eric Whitley is currently director of smart manufacturing at software company L2L.