Facilities managers looking for ways to better maintain their properties while saving money should consider investing in thermal imagery.
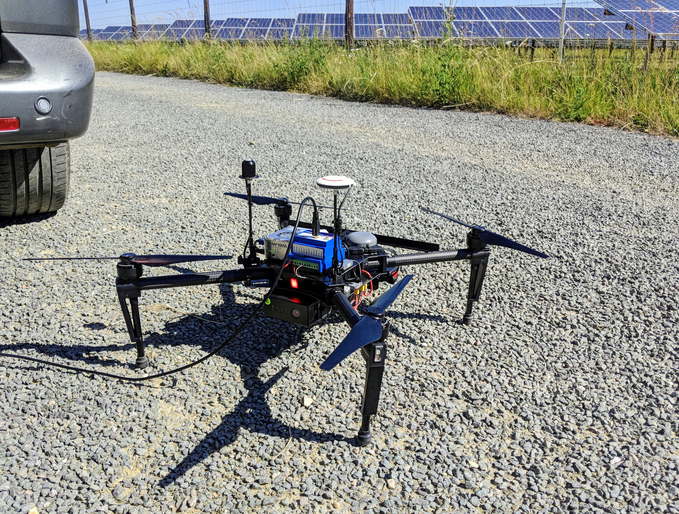
This topic was discussed during the Feb. 29 Facilities Management Advisor webinar “Getting Started with Thermal Imagery: A Beginners Guide to Thermography for Building Inspections,” sponsored by Zeitview, a company that builds advanced inspection software.
The presentation featured two guest speakers from Zeitview: Jenn Braun, senior product manager at the company’s Property Insights Platform, and Jason Kobrin, the company’s analysis and reporting manager.
Why Use Thermal Imaging?
Thermal imagery has become a common tool in facilities and building inspections to supplement visual inspections. And as Braun noted, “It helps us understand what’s going on top, outside of the building, as well as underneath and around.”
According to Kobrin, “interpreting thermal data can be tricky. What thermal cameras are capturing is the infrared radiation that’s being emitted off of the surface of the material that’s in the sight of the lens, so it’s not just the temperature.”
Thermal images can identify:
- Water entrapment: This is the primary reason thermal imaging is used, and it allows facilities managers to see thermal images of areas of moisture in the submembrane of roofs and facades not visible to the naked eye.
- Heating, ventilation, and air conditioning (HVAC) efficiency: If there are areas where hot or cool air is escaping the building’s exterior, rooftop units can be compared with each other to see if there’s a problem like an electrical issue.
- Rooftop solar anomalies: Thermal imaging can detect a lack of temperature or hot spots of specific photovoltaic (PV) cells or the PV system’s inability to operate at its maximum capacity because of an outage or another issue.
How Is Thermal Imagery Best Captured?
Kobrin explained that American Society for Testing and Materials (ASTM) standards say that thermal images should be captured:
- After dark
- When the roof has been dry of snow and rain for at least 24 hours
- Only on non-metallic and non-gravel ballasted roofs
Additionally, there are two ways data can be captured, according to Braun:
- Drone: This method is great for facilities with larger rooftops or multiple small rooftops that are close together. It keeps people off the roof until hazards are identified, and results can be delivered quickly.
- Hand-held thermal cameras: These are easy to use and great for spot assessments on smaller roofs. However, they require people to be on the roof, there might be a delay in getting results, and the process can be time-consuming for large rooftops.
How Can Companies Save Money Using Thermal Imaging?
“Getting these inspections earlier on is very important not only to the cost of repair, the cost of replacement but for the entire inside of the building,” Braun said, giving an example of a leaky ceiling.
Thermal imaging allows for preventive maintenance and early detection so roofs can simply be repaired rather than replaced. This is possible because thermal imaging will identify areas prone to water accumulation, including water ponding.
“Water ponding has a distinct pattern usually amorphic so typically no straight lines when you see it under the membrane,” Kobrin said, adding that a trained professional can tell the difference between ponding and other issues like an insulation problem; HVAC, electrical, or mechanical problems; or energy loss.
Moreover, it’s cheaper to repair rather than replace because the cost of a complete roof replacement would be $80,000 to $140,000 for an average 20,000-square-foot commercial facility roof, according to the presentation’s slideshow.
Learn More
To get more information on how to identify areas prone to water accumulation, the thermal inspection process, identifying false positives, getting secondary verification of issues, and mitigation strategies, watch the full webinar on demand for FREE by clicking here. Also read a “Back to Basics” article on determining whether to repair, restore, or replace your roof here.