Facility maintenance teams are on the brink of a transformative year in 2025, with emerging industry trends shaping how they manage resources and technology. With an aging workforce and growing operational challenges, facility maintenance teams must adapt to remain effective and resilient.
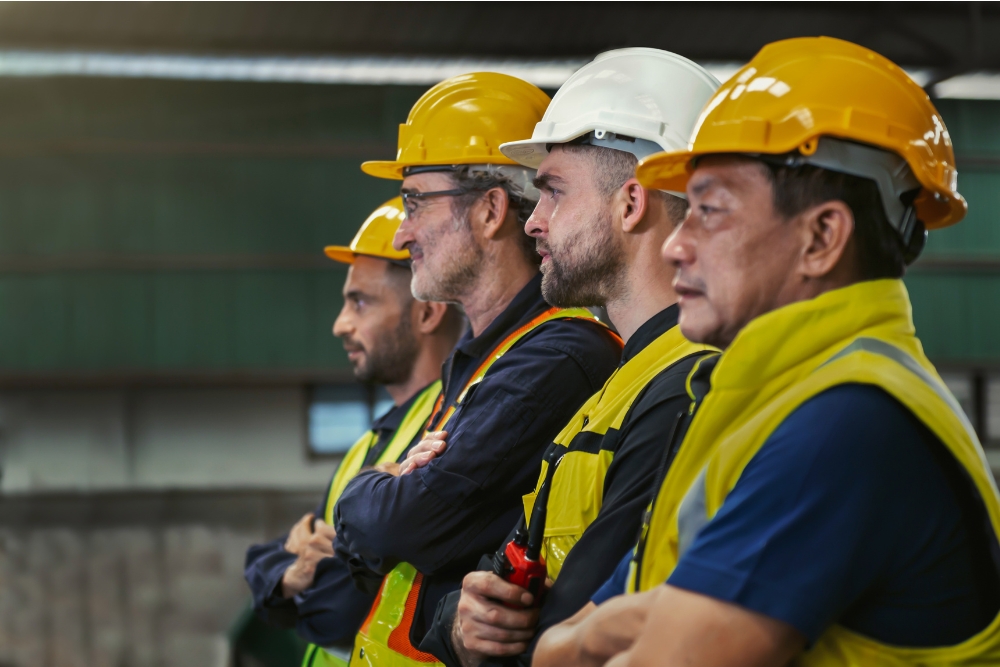
From preserving institutional facility knowledge to navigating supply chain disruptions and leveraging artificial intelligence (AI) responsibly, the coming year will test how well maintenance teams can align their strategies with these emerging trends. Below are the top predictions for how facility maintenance teams will tackle these challenges in 2025.
Institutional Knowledge and Workforce Dynamics
With the workforce aging and fewer people entering maintenance roles, companies are facing a critical need to document the knowledge held by their most experienced technicians. While this issue has been on the radar for a few years, 2025 may see more proactive solutions for capturing this tribal knowledge to streamline onboarding and ensure new, more novice technicians can ramp up quickly. Organizations must also prioritize efficiency, leveraging tools and technology to maximize the output of their existing teams.
Integrated Tech Stack and the Rise of Connected Systems
Facility maintenance teams are shifting away from being perceived as a cost center and instead becoming increasingly recognized as a strategic function critical to overall business success. In 2025, businesses will prioritize bringing maintenance out of a silo and gaining visibility into their operations. To do this, they will not only invest in dedicated facility maintenance software that is easy to use, driving frontline adoption and surfacing reliable data insights, but they will also look specifically for solutions that integrate seamlessly with other core business systems. This includes connecting facility software with Internet of Things (IoT) sensors for a more comprehensive look at asset data and maintenance history, and syncing enterprise resource planning (ERP) systems to streamline procurement workflows, improve parts management, and reduce inventory costs.
Compliance, Safety, and Regulatory Preparedness
With increasing regulatory requirements, audits, fines, and operating costs, organizations will place greater emphasis on implementing proactive safety protocols and leveraging technology to ensure regulatory compliance within their facilities. They will look for solutions that help these teams operate in adherence with regulatory standards, log asset and maintenance history, and streamline audit preparation. Collaboration between facility maintenance and safety teams will create better alignment across their processes and technology to mitigate risks, avoid fines, and enhance workplace safety.
Parts Shortages and Supply Chain Disruptions
Parts shortages and supply chain disruptions will persist, driving up costs and forcing facility maintenance teams to rethink their inventory management and procurement strategies. The increasing cost of spare parts and unpredictable lead times will push organizations to adopt more proactive and innovative strategies for managing these challenges. Facility maintenance teams will look to better record spare part usage data to inform forecasting, identify opportunities to reduce part costs across vendors, and minimize lead time for critical parts that risk prolonging equipment downtime. Technology vendors will play a crucial role in empowering organizations to mitigate supply chain risks, reduce inventory costs, and keep critical spares in stock.
A More Mindful Approach to AI in Maintenance
Recent advances in AI have generated significant buzz across the maintenance and manufacturing industries. This will continue into 2025, but organizations will adopt a more cautious and strategic approach. They will prioritize the quality of the AI models and carefully consider the potential repercussions of faulty AI outputs. They will also think about the best AI use cases for their unique position and prioritize functionality as a whole in evaluating vendors. In 2025, successful adoption of AI in maintenance will depend on organizations ensuring that it aligns with their business goals, operational needs, and regulatory requirements.
As facility maintenance teams prepare for 2025, it is clear that the industry is entering a transformative era defined by integrated technology and an evolving workforce. By proactively leveraging innovative solutions, fostering collaboration across departments, and aligning technology investments with strategic goals, facility maintenance teams can better address current obstacles and ultimately help drive business success. By focusing on these priorities, maintenance teams can not only meet the demands of a changing industry but also solidify their position as a critical component to overall business growth.
Bryan Christiansen is the founder and CEO of Limble CMMS. Limble is a modern, easy-to-use mobile CMMS software that takes the stress and chaos out of maintenance by helping managers organize, automate, and streamline their maintenance operations.