Maintaining a boiler in top operating condition will yield significant dividends to your facility, but often there are early warning signs that your boiler is in need of attention. So, what are some of these warning signs?
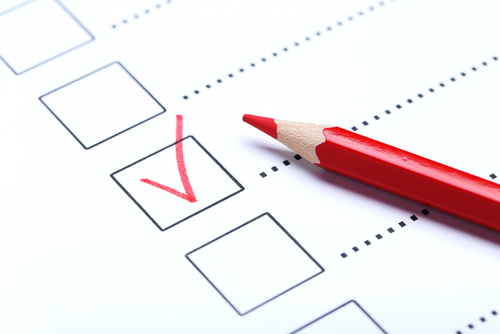
In this article, we’ll examine six indicators that your boiler may require maintenance or repair. Additionally, we’ll discuss some preventative maintenance tips to ensure your boiler is operating at its peak efficiency.
1. Elevated Stack Temperatures
The first common signs that your boiler may need maintenance are elevated stack temperatures at the same firing rate and operating steam pressure or hot water temperature. Figure 1 shows the relationship between stack temperature, excess air (oxygen or O2 in the flue gas), and combustion efficiency.
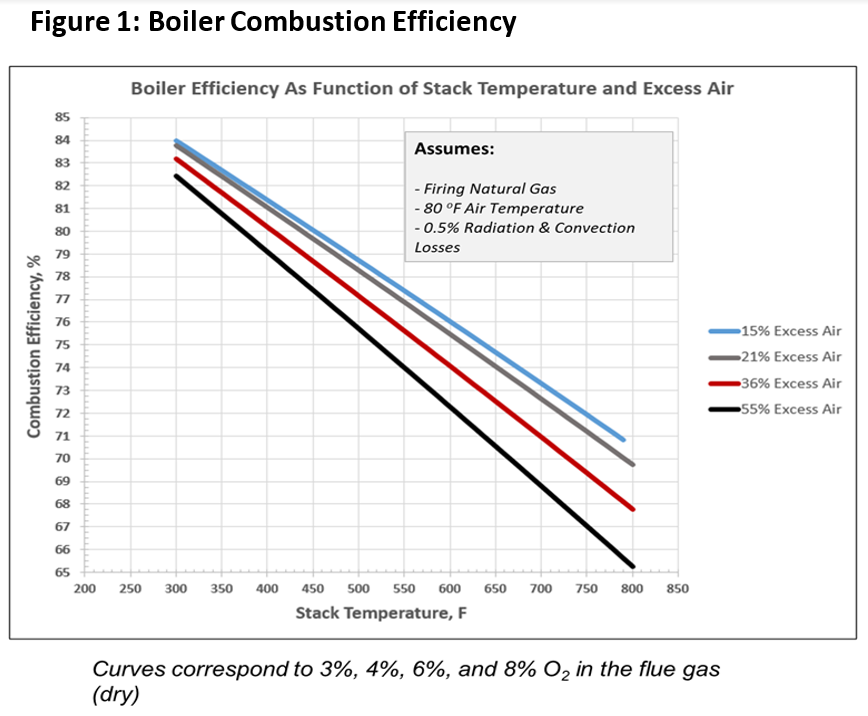
When first commissioned, your boiler was likely in a clean condition, free of appreciable soot and scale. The service technician who set combustion tuned your boiler to provide high efficiency while providing safe and reliable operating conditions. Over time, however, boiler stack temperatures at the same load and operating conditions can change:
- Scale can build up on waterside surfaces due to poor water quality;
- Soot can accumulate on fireside surfaces due to improper combustion, causes for which we will touch upon; and
- Burner component failure or changes in commissioned fuel and air settings can occur.
Waterside Scaling
Good water quality begins with proper water chemistry, both in the feedwater and boiler water. However, power water quality can create scale buildup in boiler tubes. The associated fuel loss with this buildup is depicted in the following table:
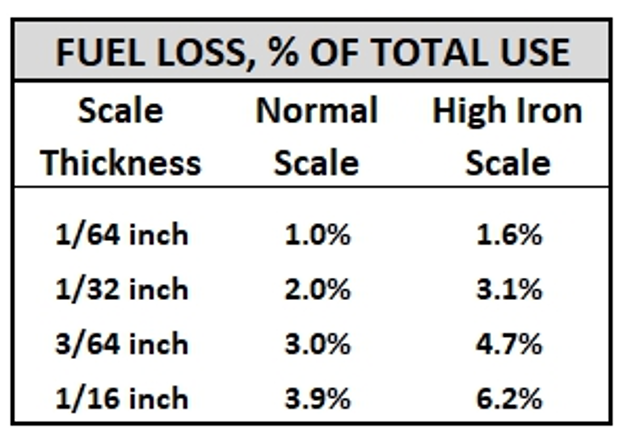
Boiler manufacturers and water quality experts can provide recommended maximum concentration levels of contaminants in the feedwater and boiler water, itself. The list of contaminants often includes dissolved oxygen (which leads to pitting and corrosion), pH, hardness, dissolved and suspended solids, alkalinity, iron and copper, and organic compounds.
Waterside surfaces should be inspected periodically and regularly for scale buildup and signs of corrosion of pitting. Other system components including water softeners, feed tanks and deaerators, pumps, valves, and chemical feed systems should be inspected and maintained on a regular basis. A regular boiler blowdown schedule of the boiler water, water columns, and sight gage glasses should be conducted.
Fireside Sooting
Sooting of boiler fireside surfaces is often the result of poor combustion or flame impingement, thereby causing flame quenching. In addition, elevated levels of carbon monoxide and other unburned hydrocarbons can result.
Whether due to changes in environmental conditions (seasonal or otherwise), changes in fuel-air mixing from originally set values, or other reasons, the sooting of fireside surfaces will result in poorer heat transfer and lower boiler efficiency.
Soot buildup in a firetube-style boiler requires cleaning to maintain good heat transfer. Similar to scale buildup on waterside surfaces, boiler efficiency loss in the range of 3%-6%, or even greater, can be expected with a sooted-up boiler.
A “rule of thumb” guideline is that for every 40-degree increase in boiler stack temperature, boiler efficiency is reduced by approximately 1%. While this may not sound like much, a 120-degree increase in stack temperature can result in an efficiency loss of 3 percentage points. Compared to a clean boiler originally operating at 80% efficiency with an annual fuel bill of $200,000, the sooted boiler can translate into spending an additional $9,800 in fuel annually.
In addition to periodic inspection of boiler surfaces, the boiler-burner should be inspected for any signs of component degradation or failure, control linkage/device changes, refractory degradation, buildup of debris on the combustion fan surfaces, filter cleanliness, and more. Keep an observation on the flame in the furnace through the rear sight port of the boiler to see if there are any marked changes in flame shape and color.
Components out of Adjustment or Failure
As with all mechanical equipment, burner- and boiler-related components will wear, settings will slip, or components can fail over time.
For example, fuel and air metering and control devices can “work their way” out of adjustment. Burner orifices and fuel delivery ports can degrade, come loose, or fail completely. Other potential sources of degradation and failure include the flame retention diffuser and burner-boiler refractory liners. Besides potential changes in stack temperature, often these sites of concern will manifest themselves in abnormal flame geometry or color, as viewed from the rear sight port of the boiler.
Much of the necessary inspection and maintenance work can be conducted by trained plant personnel. However, when it comes to detailed inspection and maintenance of the burner proper and the fuel-air control and delivery systems, these activities should only be performed by experienced and authorized boiler-burner service agents.
2. Abnormal Noise or Vibrations
While there are always vibrations and some sounds emanating from a boiler in operation, a warning sign that your boiler is no longer operating properly is quite evident. Panting and pulsing, screeching, howling, visible signs of excessive vibrations, and shaking are an indication that something is awry. Often these objectionable events are signs that combustion settings have changed, that there are issues with the stack breeching and/or draft control system, or that a failure has occurred with the burner head and fuel-air delivery components.
When any of these conditions occur, the boiler should be shut down and a service company should be contacted immediately. Often, a simple tuning of the burner is all that is required. In other cases, more dramatic maintenance and repair is needed.
3. Leakage & Corrosion
Waterside corrosion of materials and leakage of steam or water onto the boiler room floor is a sure sign that your boiler is in need of attention. Ask yourself these questions:
- Have your fuel bills increased without any significant change in load?
- Have you noticed that there is a reduction in condensate return and that there is a need for more makeup water than usual?
- Are your steam traps in good working condition?
- Are you seeing heavy corrosion and pitting on boiler tubes and other waterside materials? Are weld joints failing?
- Are you noticing water on the floor around the boiler?
- Is steam escaping from boiler gaskets, doors, or lagging?
These are sure signs that your boiler is in need of attention and possibly improved water quality.
4. Frequent Alarms & Abnormal Shutdowns
There are a number of safety and control devices and systems on your boiler. These control and safety devices range from flame monitoring to controlling water level in the boiler. Depending on the level of safety designated for the given device, a fault or trip in one of these devices will typically shut the unit down and possibly lock the unit out until the fault has been rectified.
Among the most serious fault issues are “low water” conditions and frequent flame monitoring shutdowns accompanied by a lockout condition. Often, these faults are indicated on the boiler Primary Flame Safety Device (PFSD) or another fault annunciation system located in the boiler control panel, in the operator control room, or another location.
When these faults occur, an experienced and authorized service company should be notified immediately to inspect and rectify the problem. In-house personnel should not attempt to make combustion/flame adjustment or modifications, and under no circumstance should in-house personnel attempt to dismantle and clean primary safety devices such as low water cutoffs and over-pressure safety devices.
5. Inability to Satisfy Demand Over Time
Another sign that your boiler may need attention is the inability to satisfy plant requirements, even though peak demand hasn’t changed. Low water temperature and/or steam pressure are other signs.
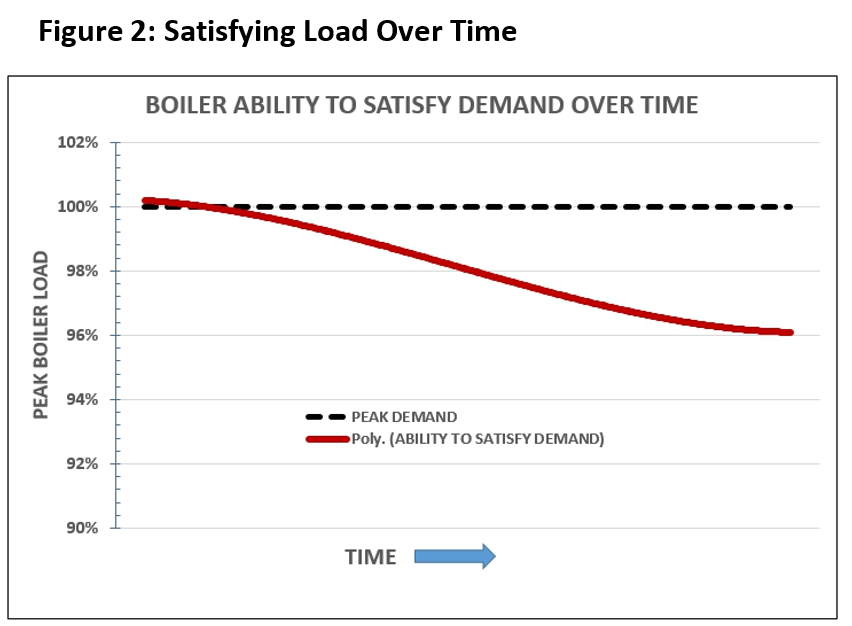
Is it taking longer to reach pressure or temperature? Similar to rising stack temperature, this may be a sign that the boiler is scaling or sooting up and that its ability to transfer fuel energy to the boiler water is being impeded. It may be time to perform a good boiler cleaning, check steam and/or hot water delivery components, and more.
6. Unfamiliar & Foul Smelling Odors
Because fuel and heat are involved in making steam or hot water, there is always the potential for leaks and overheating of materials. Some are more serious than others.
For example, leaks in fuel delivery systems are sometimes easy to detect by odor, but other times, they require leak detection equipment. When firing fuels such as natural gas or propane, the boiler-burner fuel train should be periodically but routinely lead tested to ensure that fuel gas is not leaking into the boiler room. Obviously, this can present a very dangerous situation. Burning, deteriorating gaskets are another source.
Of greater concern, leaks such as carbon monoxide (CO) through boiler casings or stack/breech joints may not be so easily detectable through smell. CO is itself colorless, tasteless, and odorless, and it is produced in the combustion process. In well-tuned and -operating burners, the CO produced in the combustion process is an intermediary step toward being converted to carbon dioxide (CO2). The flue gas should contain zero or near-zero CO. However, this is not always the case due to a variety of causes. Therefore, it is recommended that:
- Combustion be checked at least semi-annually by a qualified boiler-burner service agent and the unit be retuned if necessary, or any defective parts leading to the elevated CO levels be replaced.
- Your boiler room is equipped with a CO detection and alarm system that will not only annunciate that CO levels in the boiler room have exceeded a specified value, but will shut down the boiler and fuel supply until the issue can be remedied.
Conclusion
In closing, these are just a few of the early warning signs that your boiler and boiler system may need attention. As always, any required maintenance work which entails setting combustion or repairing or replacing safety controls and related devices should be performed by a qualified and bonded boiler-burner service agent.
Keeping an eye on these early warning signs while performing routine and periodic inspections and maintenance will provide peak operating efficiency and a long boiler life.
Mike Valentino is a technical consultant for the American Boiler Manufacturers Association (ABMA). Since its founding in 1888, the ABMA has advocated for the safe production and operation of boilers, facilitated advances in energy efficiency, and provided solutions for its member companies.