Cooling towers play a critical role in both indoor climate control and process cooling systems. Ensuring a high-quality water supply for these components enhances their efficiency, extends their lifespan, and simplifies maintenance.
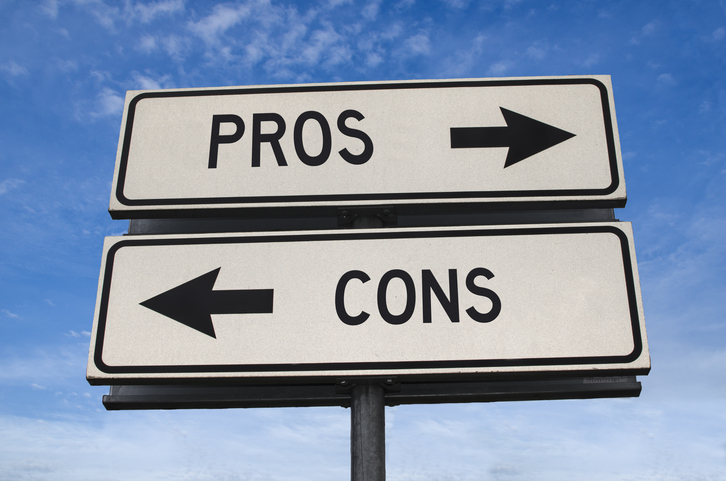
Municipal-supplied or well water has historically been the most common source of makeup water for evaporative cooling systems. However, concerns related to water scarcity and increasing water costs are leading some building owners, engineers, and facilities managers to seek alternative sources of water and treatment for their evaporatively cooled systems. Options include gray water reuse, rainwater capture, makeup water pretreatment systems, and blowdown reuse systems.
The various makeup water sources and treatment systems have potential advantages and disadvantages. What’s best for a specific application depends on the available makeup water source(s), the evaporative cooling equipment being used, and the process that the cooling system serves. This article addresses the water quality of various makeup sources and the pros and cons of some treatment systems.
EVAPCO’s Water Analytical Services, in Taneytown, Md., was established to analyze makeup and recirculating water associated with evaporatively cooled systems. An example of a makeup water report can be seen below:
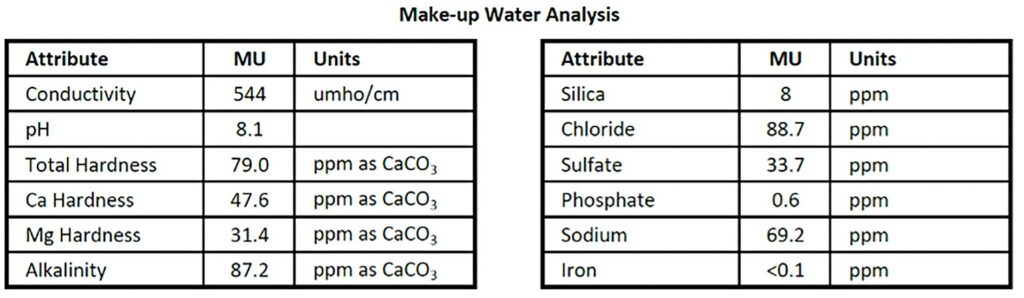
Analyzing site-specific makeup water is a good first step for contractors, engineers, and facilities managers interested in maximizing equipment service life and water efficiency. This type of analysis provides an understanding of what type of treatment program might be required to optimize operating cycles of concentration in their evaporative system. Further, the makeup water analysis can help determine whether upgrading the materials of construction from galvanized steel to 304 or 316 stainless steel can help save water.
One of the factors to consider while weighing makeup water treatment options is the source of the water. Various sources present different benefits and challenges.
Municipal Water
Municipal (city) water supply is the most common makeup water source for evaporative units in hospitals, hotels, schools, data centers, and commercial buildings.
Pros: Typically, municipal water sources offer consistent water quality, which simplifies the water treatment program. It’s also a very convenient source of makeup water because city water is already piped to the building.
Cons: City water can be more costly than other makeup water alternatives, and there may be connection fees. Also, the local municipal water treatment plant may limit the amount of water that’s available to new facilities.
Well Water
Well water can also be used to supply makeup water to an evaporative unit. This is more common at production facilities or in rural areas.
Pros: Generally, well water is less expensive than city water and connection fees are reduced.
Cons: Well water tends to have higher alkalinity and hardness levels than city water, and this can limit water efficiency do to greater scale formation potential. Well water may also contain elevated levels of iron, manganese, or silica concentrations, and may require disinfection or filtration use in the facility or process.
Gray Water
Gray water may also be referred to as reclaimed, recycled, or “purple pipe” water.
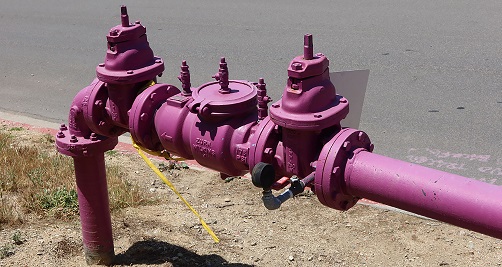
Pros: Gray water is generally less expensive than local municipal water, and may be available in areas that do not have a surplus of municipal water for new facilities or systems.
Cons: Quality of water varies more broadly compared to other sources, making the site’s ongoing water treatment more complicated. Gray water typically contains higher levels of ammonia, nitrate, phosphate, and suspended solids, which can impact corrosion or deposition concerns.
Condensate Water
Condensate recycling from air handler units can be an option for facilities that utilize large volumes of outside air in the HVAC system. Cold condensate can be a source of pure water.
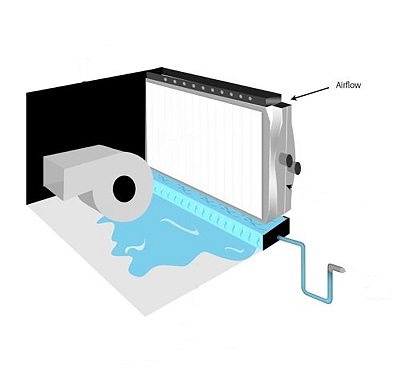
Pros: Condensate water is a source of low-conductivity water that would otherwise be sent to drain.
Cons: Requires piping and storage system to blend in with another makeup water source. It can also be corrosive to system metallurgy if not blended consistently with another source of water.
Rainwater
Harvesting rainwater can provide an additional source of makeup water in areas with sufficient rainfall. Rainwater is captured in a tank, filtered, treated, and blended as a supplemental makeup water source.
Pros: It’s “free” once the infrastructure is in place, and typically has low mineral content, making it low conductivity water for blending.
Cons: Low concentrations of hardness and alkalinity in rainwater make it more corrosive than some other sources, so blending consistently is critical. Rainwater also requires pre-filtration to reduce suspended solids before entering the holding tank. Holding tanks may require biocide to control microbiological activity.
Regardless of the water source used to supply makeup water for an evaporative cooling system, some level of pretreatment is required.
Pretreatment
Geographies with poor makeup water quality requiring low operating cycles of concentration (COC) can often benefit from the addition of a pretreatment system. Pretreatment systems can improve the quality of city, well, or gray water before it is used as makeup for an evaporatively cooled system.
Using a pretreatment system to reduce the water’s dissolved ion concentration and corresponding conductivity may allow a facility to safely increase the operating cycles of concentration. Higher operating cycles of concentration lowers blowdown water volume, which can reduce total water usage (blowdown equation shown below).

The goal of cooling water treatment programs is to create a balance between minimizing corrosion and scale potential and water efficiency (increasing operating COC) in the system. There are several different pretreatment systems that have been applied to evaporative cooling systems. Additionally, pH control (acid feed) has been utilized to reduce scaling potential to increase operating cycles of concentration. Pros and cons for several of these approaches are summarized below.
Sodium Zeolite Softener
Some vendors recommend “soft water” to minimize scale potential and increase operating cycles of concentration. Softeners exchange calcium and magnesium hardness with sodium. Using split-stream softening to reduce total hardness can be an appropriate option when hardness is the primary limiter of cycles of concentration. Makeup water sources high in alkalinity, chloride, silica, or sulfate limit the effectiveness of softeners to increase operating cycles of concentration and save water.
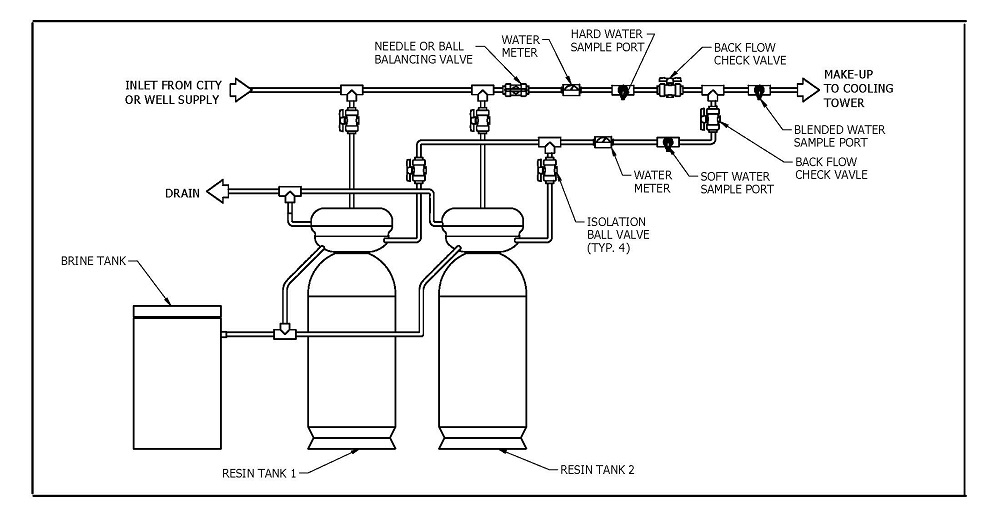
In its operations and maintenance manual, EVAPCO recommends a minimum of 50 ppm cycled calcium hardness (as CaCO3) in the recirculating water to help protect system metallurgy from corrosion. Leading equipment manufacturers do not recommend the use of 100% softened makeup water for evaporative units which include any galvanized steel as part of the materials of construction. Split stream softening, which blends some percentage of raw (unsoftened) water with the softened water, may be a safe way to improve operating cycles of concentration.
Pros: Water softeners are easy to source and relatively inexpensive. The facility may already have a softener installed for steam boiler feedwater.
Cons: There is maintenance involved with a water softener. Salt must be regularly added to the brine tank to regenerate the resin. Brine is discharged during regeneration, and some municipal sewer authorities have regulated this discharge and limited new softener applications in their jurisdictions.
There is high water usage associated with the regeneration of the resin beds. This offsets a portion of the water savings gained from higher cycles of concentration. Hardness carryover or softener upsets can create a substantial risk of rapid scale formation in the evaporative cooling system.
Resin beds are sensitive to iron fouling, and carryover of high chloride concentrations following regeneration may increase corrosion potential in the evaporative cooling system.
Capacitive Deionization
Capacitive deionization technology captures a portion of the makeup water’s dissolved ion content, yielding a low-conductivity makeup water source for the evaporative cooling system. Makeup water entering the system passes through individual cylinders which contain oppositely charged supercapacitors. A portion of all the dissolved ions (except silica) are removed from the water. Operating at 50% ion reduction allows the operating cycles of concentration to be safely doubled without an increase in scale or corrosion potential.
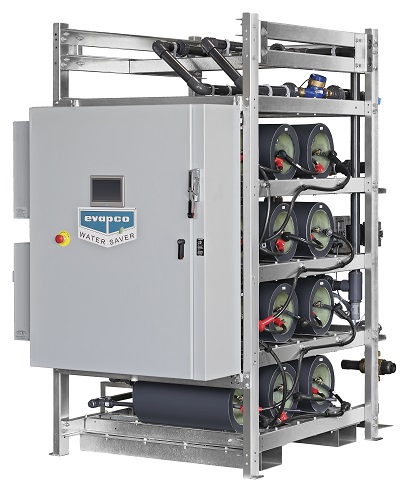
Pros: This technology lowers energy consumption when compared to reverse osmosis (RO) systems. Upset conditions do not increase corrosion or scale potential like other pretreatment systems. Recovery rates range between 75% and 85%, which is higher than most RO systems. Capacitive deionization significantly reduces the amount of water treatment chemicals purchased, handled, stored, and discharged to treat the evaporative cooling system. These systems also provide improved water quality without the need to blend other water sources back in.
Cons: This technology does not reduce silica concentrations in areas where that is the limiting factor for water efficiency. They also require routine automated, or off-line, cleaning to maintain system efficiency.
Reverse Osmosis
RO is most often found in facilities requiring high-purity water for a process application. Makeup water is forced across a semi-permeable membrane, creating a high-purity stream and a concentrated brine waste stream. Re-using the concentrated brine stream is not recommended for an evaporative cooling system as it increases the potential for both corrosion and scale. A portion of the high-purity stream can be blended with the site’s makeup water to provide a lower conductivity makeup source for the evaporative system.
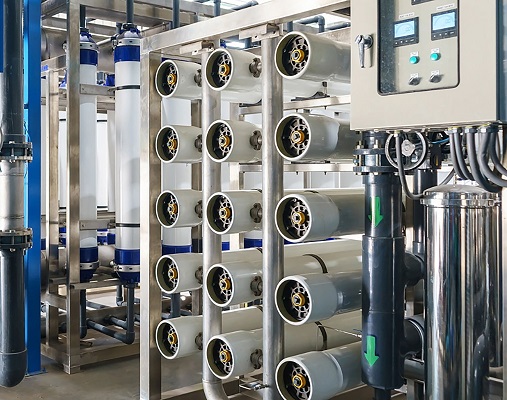
Pros: RO generates high-purity water that can be blended with raw water to create improved makeup water characteristics. It’s also effective at reducing all dissolved ions including silica concentration.
Cons: This technology comes with high energy consumption due to the need for supplemental pumping. Prefiltration and other pretreatments are often required. It also incurs a higher first cost when compared to other alternatives.
RO systems typically operate between 65% and 70% recovery, creating a meaningful waste stream. Neither 100% RO pure nor brine waters are appropriate for evaporative makeup due to corrosion and scale concerns.
Sodium zeolite softening, capacitive deionization, and reverse osmosis are pretreatment systems that have successfully been applied with evaporative cooling systems to increase operating cycles of concentration. Another chemical solution, which is not typically a pretreatment system, includes the feed of acid to reduce scaling potential by limiting the cycled alkalinity and pH in the recirculating water.
Acid Feed
Sulfuric acid is the most common acid used in evaporative cooling water treatment. Adding acid reduces both alkalinity and pH in the recirculating water. The primary reason this approach is utilized is the relatively low cost of the chemistry and feed equipment.
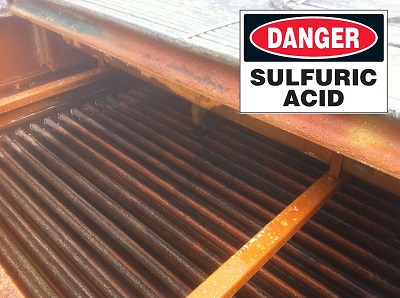
Like softening, however, the relatively low cost does not come without risk. Underfeeding or overfeeding of sulfuric acid can quickly create either scale or corrosion in an evaporatively cooled system. Therefore, site personnel should be actively engaged in the monitoring and testing of any pH control system operating on their evaporatively cooled system.
Experts recommend testing the site-specific makeup water early in the project design. This gives the end user a clear picture of their water efficiency and water treatment options. Testing water early on will also provide insight into whether upgrading materials of construction could improve ongoing water efficiency.
Blake Prescott, marketing and application engineer for EVAPCO’s Water Systems business, graduated from the University of Delaware with a bachelor’s degree in chemical engineering. He worked as a manufacturing engineer before joining EVAPCO Inc. in 2021. Prescott supports North American sales engineers and water treatment professionals.