This year, Fire Prevention Week is being observed Oct. 6-12. Fire is one of the worst things that can happen to your facility, damaging the property you have so carefully maintained and putting lives at risk. A way to gain an advantage over costly and harmful fires is properly maintaining wet and dry fire sprinkler systems in your buildings.
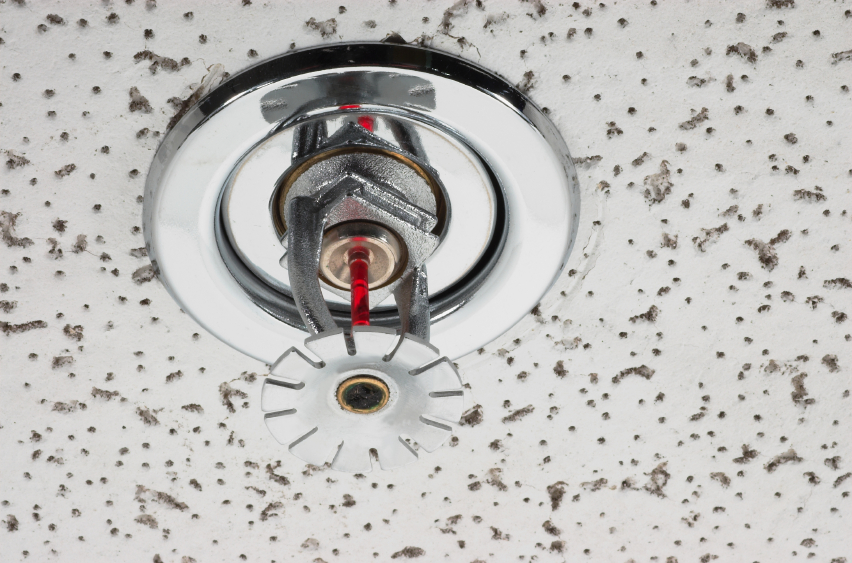
Facilities managers (FMs) should know how to maintain their fire sprinkler systems. Doing so will protect your facility and occupants, comply with legal and insurance requirements, prevent system failures, provide cost-effective maintenance, and provide risk management.
Even FMs who defer inspections to contractors should be able to identify issues proactively.
Jim McHugh, president of AGF Manufacturing, recently discussed practical tips during a webinar titled, “Extend the Longevity of Your Fire Sprinkler Systems and Minimize Maintenance.” McHugh is an active member of several industry organizations, including the National Fire Sprinkler Association (NFSA), National Fire Protection Association (NFPA), Society of Fire Protection Engineers (SFPE), American Society of Plumbing Engineers (ASPE), and American Fire Sprinkler Association (AFSA).
Here are 6 ways FMs can ensure their fire sprinkler system is properly maintained:
1. Make Sure Wet Systems Have Workable Air Vents
Wet sprinkler systems, which are constantly filled with water, are the most common sprinklers found in many facilities, including offices, university dormitories, commercial kitchens, etc.
“One of the biggest issues that affects wet fire sprinkler systems is corrosion,” McHugh said, adding that it can cause rusting and severely impact the water flow inside the pipes.
To prevent this problem, NFPA 13: Standard for the Installation of Sprinkler Systems has required wet pipe sprinkler systems to have air vents to allow as much air as possible to prevent corrosion.
“When you have trapped air pockets on wet systems, especially with steel pipe construction, you’re always worried about the steel pipe having oxygen-related corrosion.
“So, with the addition of air vents, any extra collected air is exhausted out of the sprinkler system, which cuts down on corrosion,” McHugh explained, adding this can extend the life of the system.
2. Replace Sprinkler Heads Coated with Paint or Corrosion
FMs should inspect sprinkler heads to see whether they have been affected by paint or corrosion.
“One of the biggest concerns is that a head has been coated with some form of paint that would prevent the response temperature from affecting the head,” McHugh said.
He explained that when someone paints over the sprinkler head or if there is corrosion, the temperature does not allow the glass bowl to respond. The glass bowl is an ampule inside the sprinkler head filled with a heat-sensitive liquid such as glycerin. Normally, as the temperature rises in the room, the air bubble inside the sprinkler head expands which fractures the glass, and allows the sprinkler head’s plug to be removed.
The plug inside the sprinkler head prevents water from leaking until the room’s temperature meets a specified level, usually between 135°F and 170°F, resulting in the sprinkler being activated, according to the NFPA.
“The tip cap, which is that area above the plug, is then ejected and the air can flow out and water then comes out behind that,” McHugh explained.
Also, different temperature ratings on sprinkler heads respond to different temperature rises in rooms.
To learn more about temperature ratings as well as preaction systems that are based on heat detection devices, read “Back to Basics: 4 Types of Sprinklers to Consider For Your Facility,” on Facilities Management Advisor.
3. Empty Low Point Drains in Dry Systems
While most facilities have wet sprinkler systems, FMs should be aware that they should have a dry sprinkler system if required by code in areas where pipes can freeze. Dry pipes are full of air or nitrogen until the system is activated.
Areas that have dry sprinkler systems include parking garages, outdoor walkways, and storage units.
These systems have low point drains, also called auxiliary drains and drum drips, which are full of air that accumulates water molecules causing condensation.
McHugh explained that it’s important for FMs to comply with NFPA 25, “Standard for the Inspection, Testing, and Maintenance of Water-Based Fire Protection Systems,” by ensuring that condensation is removed. The requirement is based on the temperature zone the facility is in.
This can be done by closing the top valves to maintain air integrity in your system, removing the plug from the bottom valve, opening the bottom valve to drain out any accumulated moisture, closing the bottom valve, putting the plug back in, and then opening the top valve back up.
“You have to do that as often as you can to prevent these low point chains from freezing and breaking.
“It is one of the single biggest maintenance problems on all dry and preaction systems in the fire sprinkler industry,” McHugh explained.
Specifically, NFPA 25 recommends that the drains are emptied daily especially when the temperatures fluctuate above and below freezing.
4. Prevent Control Valves from Being Tampered with or Being Closed
To prevent the backflow of sprinkler water into the water line, FMs should do regular inspections to help prevent system failure.
While control valve sprinkler systems have a 96% success rate, McHugh said that of the 4% failure rate “the greatest percentage is due to tampered or closed control valves.”
To prevent this, he said that systems should be built with precautions, such as installing a yellow indicator, to indicate if the valve is in the open or closed position.
McHugh said that this is especially important where control valves are in public areas.
As an example, McHugh mentioned that in the Citizens Bank Park in Philadelphia, where the Philadelphia Phillies baseball team plays, he said that he has seen people waiting to buy a beer turn the valve handles, but they have plugs in them to prevent the valve from tripping.
5. Test and Drain Valves
Nothing is worse for FMs than to find out their fire sprinklers aren’t working properly. FMs need to follow the NFPA 25 that dictates how a fire sprinkler system should be maintained through testing.
“In this case, the person would rotate [the] handle to the test position and inside that valve is a test orifice that replicates the flow of water through a ½-inch sprinkler head.
“And then that, of course, would flow a certain volume of water, which would activate the paddle overflow switch simulating the same flow as if there was a sprinkler head going off.
“This in turn would set off a fire alarm and potentially close your fire doors. This is how we can test to make sure that your system is fully functional,” McHugh said.
He explained that pressure relief valves are required on all wet systems to handle thermal expansion as well as a flow switch.
6. Maintain Pressure Gauges
FMs need to ensure that their sprinkler systems have the correct water pressure.
McHugh said that pressure gauges are required to be on pressure relief valves, which are the red handle valves that are required on all wet sprinkler systems to handle thermal expansion.
“You are required to have pressure gauges on both the supply side so that you know the inbound water pressure coming into a fire sprinkler system, [and] you need to have pressure gauges on the system side of all control and check valves,” McHugh said, adding that each floor should have the right pressure to supply individual sprinkler systems and relief valves.
Additionally, these gauges must be replaced every five years.
Learn More
Also discussed during the webinar were details about the impacts of corrosion, visually inspecting sprinkler heads, different types of air vents, dry air generators, nitrogen generators, corrosion monitors, and the cost of a false system trip. To learn more, watch the full webinar here.