The University of Connecticut (UConn) recently made headlines after its Huskies basketball teams fought their way to the March Madness Final Four games for both men and women. Ultimately, the men’s team won their NCAA tournament and became rare back-to-back champions.
There’s no wonder UConn is known as the “Basketball Capital of the World.” However, sports isn’t the only thing the school has going for it. UConn is also highly rated among U.S. colleges and universities, and it was named a top green school of 2024. (For details on UConn’s sustainability efforts, check out an exclusive Q&A here.)
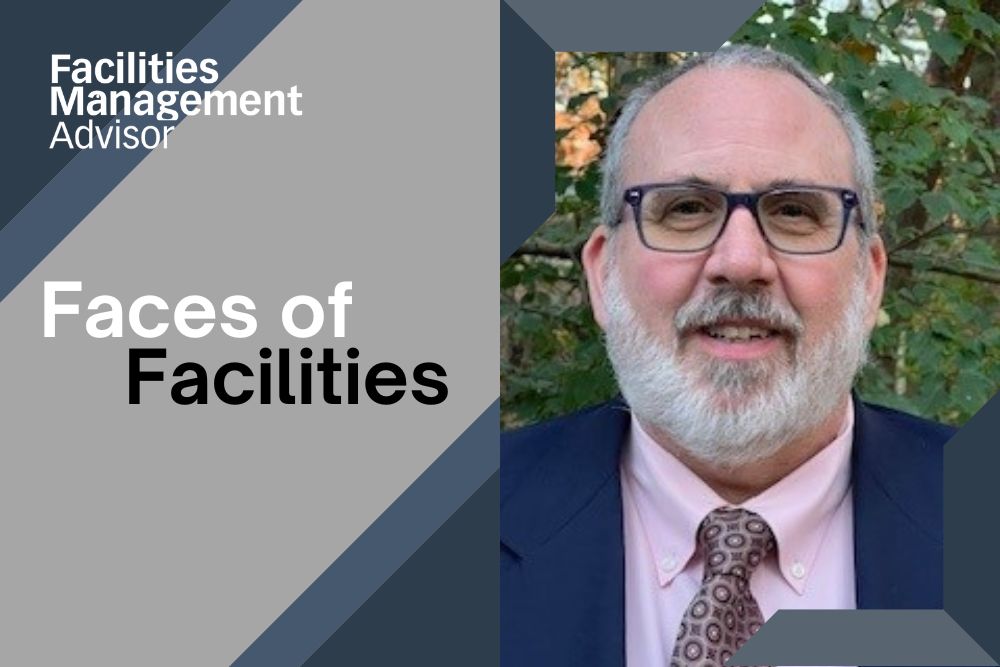
So, who helps keep campus operations running smoothly and safely at such a prestigious state school?
Meet Michael “Mickey” Gorman, associate director of trade shops in UConn’s Facilities Operations department. A proud tradesman, Gorman started at the university as an electrician and has worked there for almost 26 years.
In his current role, Gorman oversees all trade shops in Facilities Operations, which in turn, are responsible for all utilities, including medium-voltage distribution, sewer, water, steam, stormwater, chilled water, and other utilities on campus. He is also responsible for the mechanical and electrical systems across campus buildings. UConn’s main campus in Storrs, Conn., consists of hundreds of buildings and miles of utilities under and above ground. UConn also has multiple regional campuses that Gorman is involved in at a lesser level.
To learn more about Gorman and his take on industry issues, please read the “Faces of Facilities” interview below:
How did you get your start in the field?
I started in the electrical field when I decided to attend a state-sponsored technical high school and graduated in 1986 when the trades were booming. About three years after graduating and working in the electrical field, I received my license and have never left the trades.
I have always been fortunate with the different companies that I have worked for and have never burnt any bridges. I found that each company had their own way of doing business, and I feel it has made me well diversified in the way that I manage.
Who is/was your biggest influence in the industry, and why?
The biggest influence would be my instructor at the technical high school I attended. He was always a positive role model and encouraged me to always learn about new ways as the industry is always changing. He gave me my first break by setting me up to work for an electrical contractor while I was still attending high school using a work-study program. I still talk with Mr. Peters occasionally to this day, and he is still an outstanding person.
What’s your best mistake, and what did you learn from it?
My best mistake is that I have never said no to taking on more duties and responsibilities. At times this became overwhelming, but it has taught me how to manage time and resources. It has also made me versatile in many areas in facilities management. This has made me qualified for the position I am in today, and made it possible to understand how each shop works that I am responsible for.
What are some of the biggest facilities management issues at your organization?
Having to understand all systems in my position can be challenging at times. One of the largest challenges facing our department has been the need for more employees to meet the growth of our campuses, which has been substantial in recent decades at the flagship and regional locations. I would think this is an issue for most organizations, given that doing more with less has become more necessary in the industry.
What’s your favorite part about working in the industry?
The number of different systems we have is an exciting part of my job. I am never bored with the number of solutions that we must come up with daily.
On any given day, we can be dealing with a 13,800-volt power outage that may involve a transformer replacement, and the next day may be a water main break under a main campus road in the midst of a Nor’easter snowstorm. It is understood that this is part of the job, and we have learned how to deal well with these circumstances.
What changes would you like to see in the FM industry?
I would like to see more employees forming specialty groups for repairs in the high-tech areas on campus. Not only would this increase our workforce, but we would also be able to respond quickly to these issues to minimize interruptions in the department’s operations. This also would be a more efficient way of doing business.
How can company leaders make facilities management a value within their organization?
First, they need to understand the importance of facilities systems and how quickly a failure can cause interruptions in daily operations. A failure can run into high costs associated with what it may affect, so it is valuable that they understand that being proactive instead of reactive will achieve cost savings in the future.
Where do you see the industry heading in five years? Are you noticing any major trends?
I believe that automation will become even more prevalent in the future, as I have seen it continuously grow in the last 25 years that I have been at UConn.
There will be more controls at our fingertips using our laptops to run most mechanical systems in our environment. The installation of these controls system will be expensive, but will save money in the years to come through energy incentives and time spent with troubleshooting systems.
What are you most proud of?
Being able to keep our campus operational during some extreme emergencies having to do with power outages, water main breaks, snow removal, etc. This can sometimes be very challenging to avoid class closures or delays, but is a necessity to achieve because this can affect so many in the university’s community.
Do you have any advice for people entering the profession?
- Don’t let some of the people discourage you; many people appreciate what we do.
- Take advantage of training opportunities as often as possible.
- Always treat everyone with respect, the same way that you want to be treated.
- Try not to be overwhelmed during emergency conditions, and focus on making informed decisions using resources available.
Anything else you’d like to add?
I want to say thank you to this industry. I enjoy what I do, and on some days looking over the campus from a rooftop, I feel proud to be in this profession.
Are you or a colleague an FM professional interested in being profiled for the “Faces of Facilities” series? Please contact Editor Joe Bebon at JBebon@BLR.com.