There are obvious warning signs indicating a commercial elevator needs maintenance and regular inspections. Failing to maintain an elevator is not just a safety issue but also a violation of the law, including Americans with Disabilities Act (ADA) guidelines, which require specific elevators based on facility type and size and number of floors.
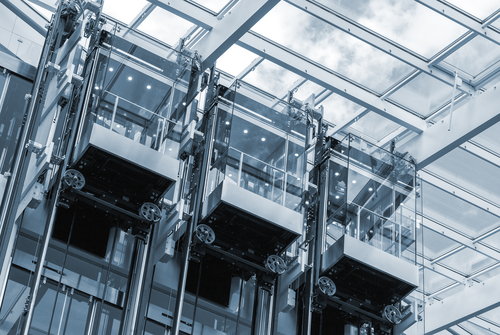
Unless the building’s facilities management team has licensed elevator inspectors, facilities managers should contact professionals to regularly inspect their elevators. Such inspections are usually part of a contract with an elevator maintenance company.
While the Occupational Safety and Health Administration (OSHA) requires elevators to be thoroughly inspected at intervals each year, several elevator companies recommend a minimum of four inspections annually. However, every state has its own rules regarding elevator inspections.
Even if you regularly inspect your elevator, be aware of the signs that your elevator needs additional maintenance and another inspection.
1. Makes Strange Noises
While older elevators tend to make more sounds than modern ones, pay attention to strange noises like grinding, squeaking, and scraping. This could indicate problems with the motor, gears, pulleys, or compression chain. These types of sounds should be investigated by a professional immediately to lower repair costs and lessen the time the elevator will be out of service for repairs.
2. Odd Movements and Vibrations
Unusual movements, like jerking, can injure occupants and lead to elevator failure. These movements could be caused by improper lubrication, worn-out components, misaligned pulleys, or issues with the motor or drive system. Additionally, odd elevator vibrations can be caused by “poorly aligned guide rail joints, eccentric pulleys and sheaves, systematic resonance in the electronic control system, and gear and motor generated vibrations,” according to a scholarly report entitled “Vibration Problems in Lift and Escalator Systems: Analysis Techniques and Mitigation Strategies.”
3. Has Midlevel Stops
When the floor of the elevator cab isn’t level with the floor outside of it, it creates a potential trip hazard. The two floors should be within ½ inch of each other. The easiest way to determine this is to draw the sole of your shoe across the landing. Midleveling is usually caused by brake issues but can also be caused by moisture, temperature, electrical voltage, and overcrowding of the elevator car.
4. Door Problems
Common problems include doors that don’t open or close correctly, get stuck, or take longer than usual to open or close. Other issues are caused by door reopening devices, the most modern of which are infrared safety curtains that scan areas adjacent to the door and automatically reopen it when the presence of an object is detected. Abuse and wear and tear can also cause issues with elevator doors.
5. Operates More Slowly
You might notice that the elevator takes more time to arrive when pressing the call button or is moving slower. The average industry wait time for elevators to respond to a call is between 20 and 30 seconds. While slow performance is often caused by a defective relay, other causes are excessive weight or aging equipment or even elevator door issues.
6. Unresponsive Buttons
Sometimes the light burns out behind a button or a malfunction causes a button to no longer work, requiring the button to be replaced. However, elevator buttons can be unresponsive because of a power supply issue, as well. Many elevators with “close door” buttons are nonfunctional so they can comply with the ADA, which requires elevators to be open long enough for someone with a physical disability to get inside.
Whether you called your in-house or outside elevator inspector because of strange noises, odd movements, midlevel stops, door problems, slower operation, or unresponsive buttons, determine whether it’s better to fix the problems, modernize the elevator, convert it to touchless, or completely replace it.