Back to Basics is an article series that highlights important, but possibly overlooked, information facilities management professionals should know.
Fires present a real danger to businesses, especially in workplaces where fire hazards are part of the job. According to the National Fire Protection Association (NFPA), a fire department in the United States responds to a fire somewhere every 23 seconds. No matter the cause, fire safety is everyone’s responsibility in the workplace, says OSHA.
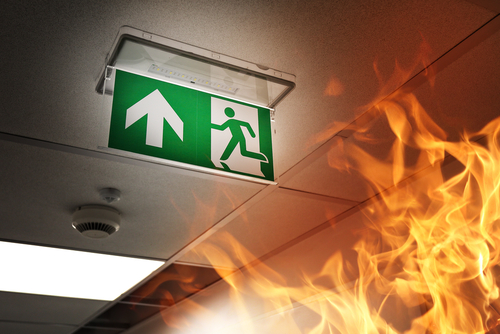
Evacuation
Employers must train workers about fire hazards and what to do in a fire emergency. A fire plan should outline the assignments of key personnel in the event of a fire and provide an evacuation plan for workers on site. Workers need to be trained on evacuation procedures, and on how to use firefighting equipment if that is expected of them.
According to OSHA, every workplace must have enough exits suitably located to enable everyone to get out of the facility quickly. When determining these exits, employers should consider the type of structure, the number of exposed personnel, the fire protection available, the type of industry involved, and the height and type of construction of the building or structure.
Exit doors must not be blocked or locked when employees are inside, and exit routes from buildings must be free of obstructions and properly marked with exit signs. Delayed opening of exit doors is permitted when an approved alarm system is integrated into the exit door design.
Fire Extinguishing
Employers are not required to provide portable fire extinguishers, but if they are provided, an educational program must be established to familiarize workers with the general principles of fire extinguisher use. Hands-on training is required if portable fire extinguishers are going to be used at the worksite.
Fixed extinguishing systems throughout the workplace are an extremely reliable firefighting tool, OSHA says. Fixed extinguishing systems detect fires, sound an alarm, and apply water or another extinguishing agent to the fire. Employers who have extinguishing systems must do the following:
- Temporarily substitute a fire watch made up of trained employees to respond to fire emergencies when a fire suppression system is out of service
- Ensure the fire watch is included in the fire prevention plan and the emergency action plan
- Post signs for systems that use gaseous agents, such as carbon dioxide or clean agents, that pose a serious health hazard
Emergency Action Plans
OSHA says that not every employer is required to have an emergency action plan, but when one is required, the plan must include several components. The plan should describe the routes for workers to use and the procedures to follow. It must account for all evacuated employees, and include procedures for evacuating disabled employees and the employees who stay behind to shut down critical plant equipment.
The action plan must include the preferred means of alerting employees to a fire emergency, and provide an employee alarm system throughout the workplace. OSHA also requires that the alarm system include voice communication or sound signals such as bells, whistles, or horns. The evacuation signal needs to be made known to the workers, and the plan should ensure the provision of emergency training.
Additionally, OSHA states that the action plan needs to remain available for employee review, and it should be reviewed by the employer with new workers and with all the employees whenever the plan is modified in any way.
Fire Prevention Plans
OSHA requires fire prevention plans to have a few minimum requirements. The first is a list of all major fire hazards, proper handling and storage procedures for hazardous materials, potential ignition sources and their control, and the type of fire protection equipment necessary to control each major hazard. The plan must also include:
- Procedures to control accumulations of flammable and combustible waste materials
- Procedures for regular maintenance of safeguards installed on heat-producing equipment
- The name or job title of employees responsible for maintaining equipment
- The name or job title of employees responsible for the control of fuel source hazards
A compliant fire prevention plan must be kept in writing, in the workplace, and be made available to employees for review. Employers with 10 or fewer employees may communicate the plan orally. The OSHA standards that require fire prevention plans include the Ethylene Oxide, Methylenedianiline, and Butadiene standards, and employers that are covered by these standards must implement plans to minimize the frequency of evacuations.
Additionally, all fire prevention plans, according to OSHA, must include housekeeping procedures for storage and cleanup of flammable materials and flammable waste. They should address handing the packing of flammable waste, and cover procedures for controlling workplace ignition sources such as smoking, welding, and burning. Recycling of flammable waste such as paper is highly recommended and encouraged.
Prevention plans must also provide for proper cleaning and maintenance of heat producing equipment such as burners, heat exchanges, boilers, ovens, stoves, and fryers, and require storage of flammables away from this equipment. The plans must inform workers of the potential fire hazards of their jobs and plan procedures, and employers should be able to review it readily. Employers must go over the fire prevention plan with new employees and all employees if the plan is altered.
For more information, click here to view OSHA’s recommendations for fire safety.